Basic Warehousing 101: Essential Tips and Processes
21 Nov 2024
|by diadmin
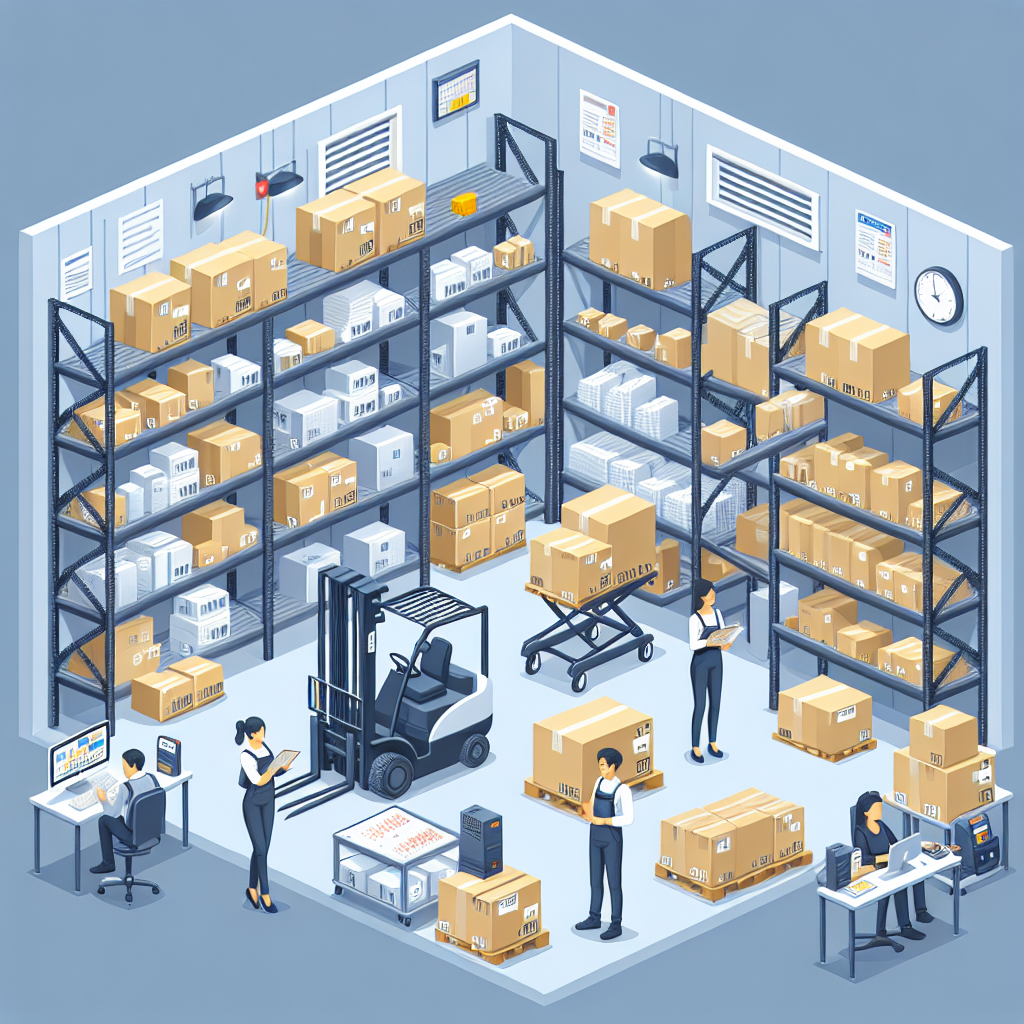
Basic Warehousing
Basic warehousing covers processes like receiving, storing, picking, packing, and shipping goods. Efficiently managing these activities is vital for smooth supply chain operations. In this article, you’ll learn about key warehousing processes, warehouse layout strategies, inventory management, and the role of technology in modern warehouses.
Key Takeaways
- Warehousing is critical to supply chain efficiency, encompassing processes such as receiving, storage, picking, packing, and shipping, all of which need optimization for effectiveness.
- Implementing a Warehouse Management System (WMS) enhances operational speed and accuracy by automating inventory management and providing real-time data insights for informed decision-making.
- Layout design and technology integration in warehouses significantly impact productivity and safety, necessitating regular reviews and updates to adapt to evolving business needs.
Understanding Basic Warehousing
The supply chain fundamentally relies on warehousing to maintain a seamless transfer of goods throughout the distribution process. Warehousing primarily involves strategically managing and housing goods until they are required for Progress, focusing on optimal storage efficiency.
In warehouse operations, numerous essential activities take place such as receiving merchandise, inventory upkeep, fulfilling orders through picking and packing practices, and executing shipments. The efficacy of these processes is crucial in upholding overall warehouse productivity and ensuring that product standards align with consumer demands by proficiently controlling the quality of goods.
Warehouse management systems (WMS) serve to refine these tasks by offering access to instantaneous data allowing for insightful managerial decisions. A myriad of WMS exist with functionalities including enhanced inventory regulation, automatic storing & retrieval mechanisms as well as live tracking. All contributing factors towards augmenting warehouse effectiveness. Bolstered by a Warehouse Control System (WCS), these features become even more powerful.
Efficient spatial planning within a warehouse significantly influences operational fluidity—reducing potential disruptions in workflow thereby expediting precise handling and positioning of products. It’s imperative when evaluating key procedures within any given warehouse setting to appreciate their interconnectivity, which ultimately dictates the triumphs realized across broader supply chain endeavors.
Key Warehouse Processes
The core of an effective warehouse resides in the optimization of its fundamental operations. Receiving, putaway, storage, picking, packing, and shipping are the six key processes that need fine-tuning for improved performance. By focusing on these aspects, warehouses can significantly boost their efficiency while cutting down on errors and operational costs.
Every step is critical to guarantee a seamless transition of merchandise within the warehouse environment from the moment it arrives until it reaches its final destination.
Receiving Goods
The commencement of effective inventory management starts with the goods reception process. It’s critical for laying the groundwork for all following activities, encompassing the transfer of items and maintaining responsibility over stock levels. To avoid incongruities within stock-keeping records and uphold customer fulfilment, best practices in this initial phase should involve meticulous scrutiny, precise recording, and early stages of inventory oversight.
Should any mishaps arise throughout the inception stage of receiving merchandise, they can result in substantial challenges subsequently like shortfalls in inventory that negatively impact consumer contentment. Efficient handling at this point does more than just safeguard warehouse operations by precluding damaged commodities from being added to stocks. It also enhances both pace and precision while averting bottlenecks at delivery points.
Put-Away Strategies
Putaway involves moving inventory from the receiving area to storage, a key step for efficient warehouse operations. An optimized putaway process reduces inventory loss, improves organization, and aids the picking process, thus enhancing overall warehouse productivity. Standardizing putaway processes maintains consistency, reduces errors, and improves efficiency.
Different putaway methods, such as those based on purchase orders, SKUs, or product types, can be leveraged to suit the warehouse’s needs. Critical factors for effective putaway include having a clear plan for inventory location, utilizing proper storage equipment, and employing technology to guide staff to optimal storage locations.
Inventory Storage
The central aim of maintaining store inventory in a warehouse setting is to safeguard goods until they are requested for orders. This procedure primarily entails strategically situating items within designated storage locations, allowing for their swift and effortless retrieval when necessary. Within the confines of an ecommerce warehouse environment, it’s common practice to house inventory on shelving units using pallets or containers, assigning specific spots for individual SKUs.
Employing kitting techniques can be instrumental in conserving valuable storage space while simultaneously reducing labour expenses. This method involves grouping products together with precision. The main objective here is not only achieving exactness during order fulfilment but also streamlining warehousing operations to avoid unnecessary tasks.
Tailoring storage choices to align with company objectives serves as a critical factor in enhancing operational efficacy. Through the meticulous organization of product placement and implementation of appropriate storage apparatuses, warehouses are well-positioned to augment their available storage capacity and bolster overall work efficiency.
Picking Techniques
The selection and retrieval of items, known as the picking process, is essential for executing customer orders. This step has significant implications on client contentment, financial success, and the perception of a brand. Among the prevalent techniques utilized are zone picking—which involves workers staying within specific sections to minimize travel distance yet may result in an unbalanced distribution of tasks—as well as batch picking—where several orders with similar products are gathered at once—and wave picking.
Deciding upon an optimal method for item collection depends on elements such as warehouse organization, nature and quantity of merchandise ordered by customers. By employing effective strategies tailored to these factors, order fulfilment operations can not only ensure near-perfect accuracy rates reaching 99.9% but also slash labour expenses by up to 40%, enhancing overall efficiency.
Packing Procedures
The warehouse places a high emphasis on packing, striving to safeguard the integrity of products while in transit without incurring excessive costs. The process encompasses both the consolidation of items for their journey and confirming that they reach their destination intact. Striking a balance is crucial. Overpacking drives up expenses, while insufficient packing can cause damage to goods. A strategic approach to packing secures merchandise while meeting shipping standards.
Ensuring that each picked item is traceable throughout the packing phase promotes order accuracy. Considering that damaged goods may dissuade 40% of customers from making future purchases, meticulous attention during packaging operations can have an indirect but significant impact on customer satisfaction and the perception of a brand.
By refining and streamlining its procedures for packaging, enterprises stand to lower these costs by as much as 30%, thereby enhancing operational efficiency and profitability within this aspect of logistics.
Shipping Operations
Ensuring that products are shipped promptly, accurately, and to the intended location is crucial for the effectiveness of the shipping process. Any postponements in sending out items result in delivery delays that can hinder business expansion. Enhancing accuracy and efficiency within these processes is a central strategy for bolstering on-time deliveries while simultaneously cutting down on transportation expenses.
Obstacles such as insufficient inventory levels, elevated costs associated with order fulfilment, and mistakes made by individuals can diminish shipping productivity. Maintaining clear communication channels with both customers and transporters is vital for guaranteeing efficient dispatches, correct cargo loading practices, and timely as well as secure product arrivals.
Benefits of Effective Warehouse Management Systems (WMS)
Warehouse management systems (WMS) enhance the speed and precision of warehouse operations by streamlining order locating, picking, packing, and dispatching processes. The data analysis and reporting capabilities offered by a WMS guide decision-making to refine operational procedures.
By replacing manual processes with automated solutions in warehouse management, a WMS boosts workflow efficiency significantly. Automated inventory management tools integrated within the WMS facilitate efficient collection and examination of data while providing instant tracking updates for orders in transit—thus improving the overall visibility of operations.
Real-time notifications and graphical data representations from many warehouse management systems empower more accurate decisions based on up-to-the-minute information. This real-time capability is integral for maintaining superior performance levels across various aspects of warehouse management.
Optimizing Warehouse Layout
The design of a warehouse impacts its operational efficiency and overall effectiveness in supply chain management. An efficient warehouse layout minimizes workflow interruptions, enhancing overall productivity. Factors impacting the efficiency of a warehouse’s physical layout include space allocation, design infrastructure, equipment, and inventory balance.
Core components to consider in a warehouse layout include receiving, storage, packing, shipping, and service areas. Different layout design types, such as U-shaped, I-shaped, and L-shaped, each affect workflow efficiency differently. Different storage methods are essential based on the types of products, influencing the final warehouse layout.
Taking advantage of technology can optimize layout effectiveness, with tools like warehouse management systems supporting operations. Regular reviews and adjustments of warehouse layouts promote continual improvement as business needs evolve.
Importance of Inventory Management
Efficient management of inventory avoids both shortages and surplus, protecting customer satisfaction as well as financial assets. The significance of warehousing is highlighted in its ability to navigate seasonal demand changes, guaranteeing product availability when necessary.
An orderly system for managing stock elevates the pace at which orders are filled, thus bolstering customer delight. Conducting periodic audits of inventory fosters precision by aligning documented stock with physical quantities on hand, minimizing variances. Employing RFID technology offers instant visibility into the whereabouts of merchandise within the warehouse, markedly enhancing the effectiveness of inventory management.
Enhancing Warehouse Safety
Safety regulations dictate that warehouse layouts must include clear exit routes and designated areas for hazardous materials. Compliance with these regulations is crucial to protect workers and prevent costly accidents. A thorough warehouse safety checklist includes setting standards, training employees, and regular hazard audits.
Regular safety meetings with employees foster awareness and enhance the safety culture. Regular equipment maintenance is vital to prevent disruptions, reduce safety risks, and minimize operational liability.
A clean and organized warehouse reduces the likelihood of accidents and machinery breakdowns, thereby improving employee morale.
Leveraging Technology in Modern Warehouses
Incorporating advanced intelligent technologies in warehouse management can markedly improve the efficiency and speed of distribution and order fulfilment processes. By adopting automation technology, not only is operational precision increased, but also the velocity at which orders are fulfilled. This allows workers to dedicate their efforts to more critical tasks. Automated storage and retrieval systems (ASRS) notably boost space optimization while simultaneously enhancing efficiency by mechanizing the process of storing and retrieving items.
The use of automated guided vehicles (AGVs) along with mobile robotics facilitates goods movement within warehouses autonomously, thereby diminishing human involvement. Drones employed within warehouse settings play a significant role in carrying out inventory assessments as well as surveying areas that are otherwise challenging to access, thus cutting down on manual labour requirements. The application of Internet of Things (IoT) connectivity provides improved control over various components involved in warehouse operations, leading to greater overall effectiveness.
Leading companies such as Amazon, Walmart, and UPS have been capitalizing on artificial intelligence alongside robotic innovations for elevating proficiency levels across different aspects like accuracy enhancement regarding safety measures or swiftness within their logistical frameworks. Harmonizing disparate technological solutions including ASRS with Warehouse Management Systems (WMS), these industry giants realize substantial refinements in workflow streamlining. Concurrently implementing contemporary picking methodologies equipped with automated facilities Augments both rapidity and exactitude within warehouse environments.
Outsourcing to Third-Party Logistics (3PL)
Companies can leverage significant cost savings through economies of scale by employing the services of a third-party logistics provider (3PL). The flexibility offered by 3PL services empowers businesses to modify their logistics operations in response to varying demands. By delegating logistic tasks, companies are able to concentrate on their core business activities and avoid the intricacies associated with logistics.
Engaging with a third-party logistics partner grants businesses access to specialized expertise in the field without having to commit capital towards developing internal infrastructure. Utilizing a 3PL enhances not only efficiency, but also extends the reach of companies’ logistical capabilities.
Evaluating Key Performance Indicators (KPIs)
Warehouse supervisors utilize Key Performance Indicators (KPIs) as crucial measures that enable them to understand their operational effectiveness and fine-tune processes to enhance both efficiency and cost-effectiveness. Assessing the precision of inventory helps in pinpointing variances between what is documented on books versus the actual counts of stock available. Shrinkage quantifies the monetary impact of inventory that has gone missing due to factors like theft or spoilage while carrying costs encompass all expenses associated with housing and upkeeping inventory.
The frequency with which goods are sold out and restocked within a specific timeframe is encapsulated by the rate of inventory turnover. The evaluation of performance encompasses various elements such as how quickly orders are filled, along with assessing whether they have been completed punctually, without mistakes, and without subsequent customer claims. Examining return rates—proportionate instances where customers send back purchases—can uncover underlying problems related to product quality or satisfaction levels.
Summary
Optimizing each step of warehouse processes is essential for the smooth functioning of supply chain management. Every aspect, from receipt to dispatch, plays a critical role in ensuring that goods transition seamlessly through various stages within the warehouse. The implementation of robust warehouse management systems and strategically designed layouts can greatly improve efficiency and elevate productivity levels.
Adopting cutting-edge technologies and engaging with third-party logistics providers are strategies that help simplify operations while also mitigating expenses. Warehouse managers can harness key performance indicators as tools to gain insights into their procedures, allowing them to make data-driven improvements aimed at elevating overall effectiveness and enhancing customer satisfaction. By embracing these best practices, you prepare your warehouse to adeptly respond to the dynamic requirements of today’s marketplaces.
Frequently Asked Questions Regarding Basic Warehousing
What are the key processes in warehousing?
Optimizing the critical processes of receiving, putaway, storage, picking, packing, and shipping in warehousing is essential for improving efficiency and minimizing operational costs.
How does a Warehouse Management System (WMS) enhance warehouse operations?
A Warehouse Management System (WMS) greatly improves operational processes by providing access to real-time data, optimizing workflow efficiency, and enhancing precision in the processing of orders.
As a result, warehouse management becomes more efficient and productive due to these advancements.
Why is inventory management important in a warehouse?
Efficient management of inventory within a warehouse is essential as it helps to avoid both shortages and surpluses, accelerates the process of fulfilling orders, and guarantees consistency between documented inventory figures and physical stock.
By doing so, it significantly enhances overall operational effectiveness while boosting customer satisfaction.
What are the benefits of outsourcing logistics to a Third-Party Logistics (3PL) provider?
By engaging a Third-Party Logistics (3PL) provider, companies can achieve significant cost reductions, gain increased adaptability to fluctuations in demand, and benefit from specialized logistics knowledge without the necessity of major infrastructure expenditure.
How can technology improve warehouse safety and efficiency?
Technology significantly enhances warehouse safety and efficiency by implementing automated systems like ASRS and AGVs, which optimize operations and reduce manual handling. This not only streamlines processes but also minimizes the risk of accidents and errors. To discuss your requirements, contact us.