Benefits of Warehouse Management
16 Oct 2024
|by diadmin
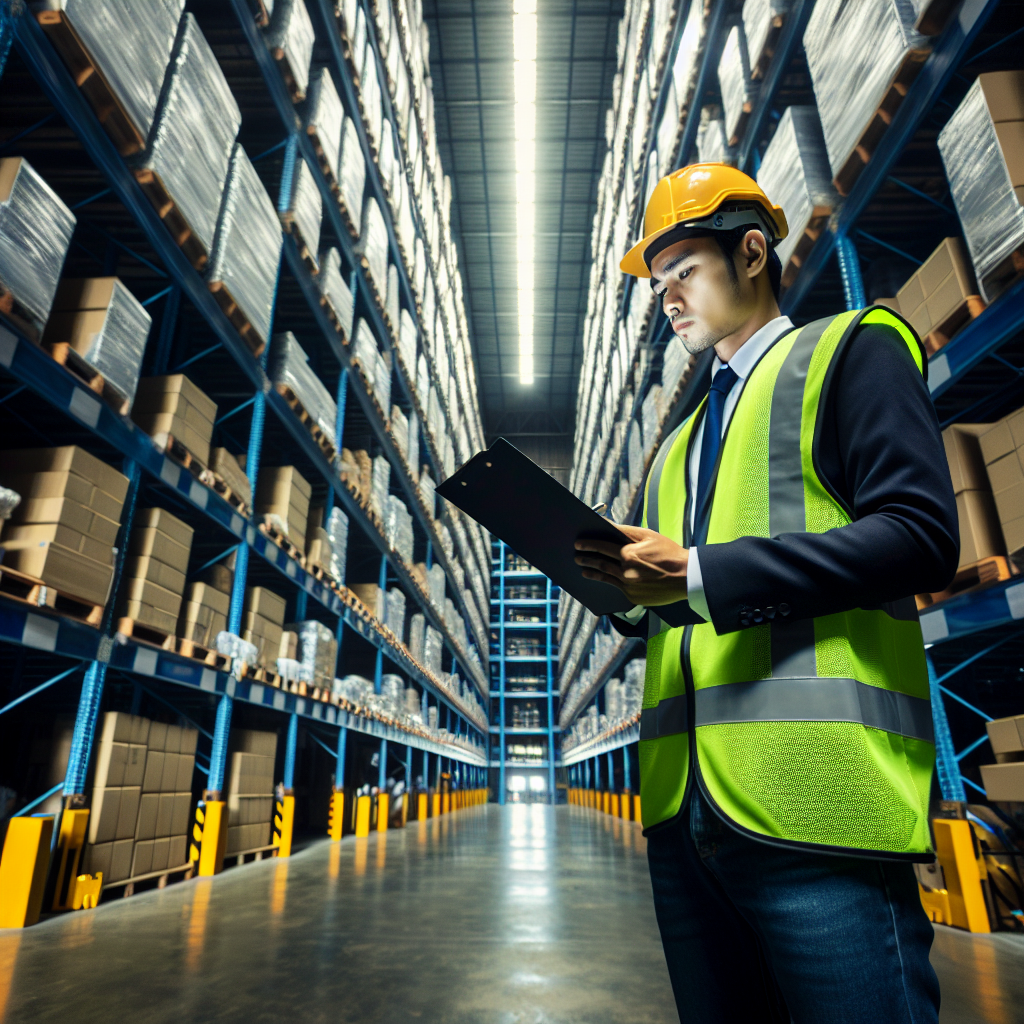
What is a Warehouse Management System?
To discuss the benefits of Warehouse management we first need to know what a warehouse management system is. A Warehouse Management System (WMS) is warehouse management software that helps run things smoothly in a warehouse or distribution centre. If your business has inventory, having a WMS is essential to keep things organized and running efficiently. It gives you a real-time look at inventory levels, making decision-making a lot easier.
Common Challenges in Warehouse Operations
Inaccurate Inventory Tracking and Management
Inaccurate inventory tracking can lead to stockouts or overstock situations, resulting in lost sales or increased holding costs. Without precise data on inventory levels, businesses may struggle to meet customer demands or tie up capital in excess stock.
Inefficient Warehouse Operations and Processes
Inefficiencies in warehouse processes can slow down order fulfilment and increase operational costs. Poor layout design, inadequate staff training, and outdated technology can contribute to delays and errors in picking, packing, and shipping processes.
High Labor Costs and Low Productivity
High labor costs without corresponding productivity gains can erode profit margins. Factors such as insufficient employee training, inadequate performance tracking, and lack of automation can result in lower productivity and increased labor expenses.
Poor Supply Chain Management and Visibility
Weak supply chain management can lead to delays, increased costs, and customer dissatisfaction. Limited visibility into the supply chain makes it difficult to anticipate disruptions, coordinate with suppliers, and optimize inventory levels across the network.
Limited Access to Real-Time Data and Analytics
Without access to real-time data and analytics, businesses may struggle to make informed decisions. This limitation can hinder the ability to quickly respond to market changes, optimize operations, and improve customer service, potentially impacting overall competitiveness.
10 Benefits of Implementing a WMS
1. Inventory Accuracy
Managing inventory can be a real headache. Without accurate tracking, businesses risk running out of stock or dealing with piles of excess inventory. This often leads to missed sales opportunities and high holding costs.
Imagine the stress of not being able to fulfill customer orders because products aren’t available, or the frustration of overflowing storage with unsold items. These issues can disrupt operations and leave customers disappointed.
Enter the WMS. This game-changing tool meticulously monitors stock levels and item locations within the warehouse. By keeping inventory accurate, businesses can perfectly align supply with demand, reducing excess stock and avoiding costly shortages. A WMS enhances inventory visibility by providing real-time tracking of products from receiving to shipping, reducing the risk of lost inventory. The result? A smoother operation and happier customers.
2. Order Fulfillment Efficiency
Managing order fulfilment efficiently is a common challenge for businesses, especially during peak seasons or promotional events when the volume of orders surges.
Without an optimized system, businesses can struggle with slow picking, packing, and shipping processes, leading to bottlenecks and dissatisfied customers.
A WMS system offers a streamlined approach to order fulfilment. By enhancing the speed of these processes, it boosts throughput, enabling businesses to handle higher volumes of orders with ease. Efficient order fulfillment also strengthens customer and supplier relationships by ensuring timely and accurate deliveries.
3. Space Optimization
Managing warehouse space efficiently is a constant challenge, as poor organization can lead to increased storage costs and the premature need for additional facilities.
When products are not organized based on size, volume, and demand, it results in wasted space and operational inefficiencies, ultimately eating into profit margins and resource allocation.
Implementing a Warehouse Management System optimizes space by organizing products intelligently. This not only improves space utilization but also reduces costs and delays the need for expanding warehousing facilities.
4. Reduced Errors
Managing warehouse operations manually can lead to frequent human errors in inventory records and order picking, impacting order accuracy and customer satisfaction.
These mistakes not only cause delays but also result in increased returns and costly rework, consuming valuable time and resources.
Implementing a Warehouse Management System automates these processes, significantly reducing errors. This leads to more accurate order processing, enhanced customer satisfaction, and ultimately saves time and money through fewer returns and less rework.
5. Improved Customer Service
Slow and inaccurate order processing often leads to delayed deliveries and increased errors, frustrating customers and damaging brand reputation.
When customers experience late or incorrect orders, their satisfaction decreases, making them less likely to return or recommend the brand to others, ultimately affecting the business’s bottom line.
Implementing faster and more accurate order processing ensures quicker delivery and fewer mistakes. By receiving their orders promptly and correctly, customer satisfaction and loyalty are enhanced, turning them into repeat buyers and enthusiastic brand advocates.
6. Enhanced Security
Inadequate security within a warehouse can lead to unauthorized access, theft, and mishandling of inventory, posing significant risks to your business.
Imagine the worry and financial loss associated with missing or damaged goods and the potential disruption it could cause to your supply chain and customer satisfaction.
A Warehouse Management System enhances security by restricting inventory access to authorized personnel and tracking user activities. This reduces the risk of theft and mishandling, ensuring your inventory remains secure and your operations run smoothly.
7. Real-time Data and Analytics
Struggling to keep track of inventory, order status, and productivity metrics? This lack of real-time insights can lead to poor decision-making and inefficiencies in operations.
A Warehouse Management System (WMS) is a type of warehouse management software that provides up-to-the-minute data on inventory levels, order status, and productivity. With this information at your fingertips, you can make informed decisions about purchasing, staffing, and operational strategies.
Imagine the impact of real-time analytics, allowing you to swiftly adjust and enhance efficiency and service levels. Embrace a WMS to transform your operations and stay ahead in the competitive market.
8. Scalability
As your eCommerce business expands, managing increased inventory and transaction volumes can become challenging, often leading to errors and delays.
These issues can hinder your ability to sustain growth smoothly and disrupt operations, impacting customer satisfaction and your business’s reputation.
Implementing a Warehouse Management System can scale efficiently with your business, handling increased volumes without the associated problems. This scalability supports sustainable growth, allowing for seamless expansion and uninterrupted operations.
9. Return Processing
Managing returns efficiently is crucial in the eCommerce industry. Without a streamlined process, returns can disrupt operations, cause inventory inaccuracies, and lead to losses.
Imagine dealing with a backlog of returns, struggling to reintegrate items into your inventory, and facing dissatisfied customers due to delayed restocking. Such issues can severely impact your business performance.
Implementing a Warehouse Management System can transform your operations. A WMS simplifies the returns process, quickly reintegrating items and updating stock levels. This ensures accurate inventory data and minimizes losses, enhancing customer service. Ready to elevate your warehouse operations? Discover how our WMS solutions can help you achieve these benefits and more.
10. Reduced Costs and Improved Profitability
Implementing a Warehouse Management System (WMS) can significantly reduce costs and improve profitability for businesses. By streamlining warehouse operations, automating tasks, and improving inventory management, companies can minimize waste, reduce labour costs, and optimize storage space. A WMS can also help businesses make data-driven decisions, identify areas for improvement, and implement cost-saving strategies.
Some of the ways a WMS can reduce costs and improve profitability include:
- Reducing labour costs by automating tasks and improving workflow efficiency
- Minimizing waste and reducing inventory costs by optimizing storage space and improving inventory management
- Improving supply chain visibility and reducing transportation costs
- Enhancing customer service and reducing returns and refunds
- Providing real-time data and insights to inform business decisions and drive growth
By implementing a WMS, businesses can achieve significant cost savings and improve profitability, ultimately driving growth and success.
Best Practices for Warehouse Management Systems
Software and Process Updates: Regularly review and update your WMS system and processes to ensure they align with current industry standards and technological advancements. This can help optimize efficiency, reduce errors, and improve overall operations.
Staff Training and Support: Provide ongoing training and support for warehouse staff to enhance their skills and knowledge. This includes workshops, seminars, and hands-on training sessions that focus on new technologies and practices, ensuring the team remains competent and confident in their roles.
Performance Monitoring: Monitor and analyze key performance indicators (KPIs) such as order accuracy, processing times, and inventory levels to assess the efficiency of operations. Use this data to identify areas for improvement and make informed decisions to enhance productivity.
Operations Improvement: Continuously evaluate and improve warehouse operations by implementing best practices and innovative solutions. This includes streamlining workflows, reducing waste, and enhancing safety measures to create a more effective work environment.
System Integration: Ensure integration with other business software and systems, such as Enterprise Resource Planning (ERP) and Customer Relationship Management (CRM) systems, to facilitate seamless data exchange and improve overall operational efficiency. This integration helps maintain consistency across the organization and supports better decision-making processes.
Implementing a Warehouse Management System
Meticulous planning and execution are vital for successful implementation. Seamless integration with existing business software and systems is crucial. Comprehensive training and support facilitate a smooth transition. Regular maintenance and updates are needed to ensure peak performance. A digital warehouse management system offers real-time visibility and control.
Choosing the Right WMS
Choosing the right Warehouse Management System (WMS) is crucial for businesses looking to optimize their warehouse operations and improve profitability. With so many WMS options available, it can be overwhelming to determine which one is best for your business.
Here are some key factors to consider when choosing a WMS:
- Will the WMS grow with your business, or will it become outdated quickly?
- Can the WMS be tailored to meet your specific business needs and processes?
- Will the WMS integrate with your existing systems, such as ERP and CRM?
- Is the WMS user-friendly and easy to navigate?
- What kind of support and training does the WMS provider offer?
- What is the total cost of ownership, including implementation, maintenance, and support?
By considering these factors and doing your research, you can choose a WMS that meets your business needs and drives growth and success.
Integration with Other Systems
A Warehouse Management System (WMS) is not a standalone solution, but rather a critical component of a larger ecosystem of systems and processes. To achieve maximum efficiency and effectiveness, a WMS must integrate with other systems, such as:
- Enterprise Resource Planning (ERP) systems
- Customer Relationship Management (CRM) systems
- Transportation Management Systems (TMS)
- Inventory Management Systems (IMS)
- Supply Chain Management (SCM) systems
By integrating with these systems, a WMS can provide a single, unified view of your business operations, enabling you to make data-driven decisions and drive growth and success.
Some of the benefits of integrating a WMS with other systems include:
- Improved supply chain visibility and coordination
- Enhanced customer service and satisfaction
- Increased efficiency and productivity
- Better inventory management and control
- Reduced costs and improved profitability
By integrating your WMS with other systems, you can achieve a seamless and efficient flow of data and processes, driving growth and success for your business.
If you are interested to take charge of your warehouse operations and see how Lofko can help your business succeed. Book a strategy call with our expert team today!