Designing a Warehouse Layout That Works: The Blueprint to Productivity
16 Oct 2024
|by diadmin
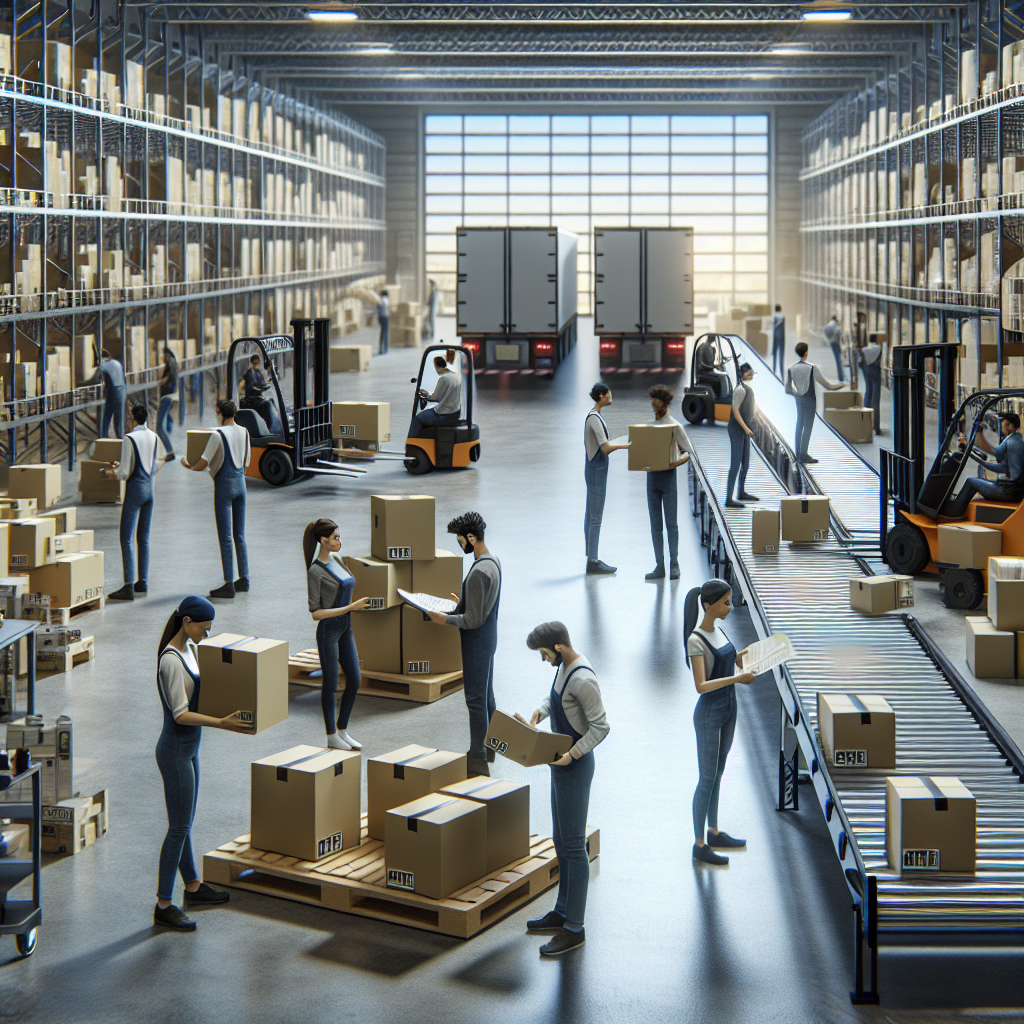
In the fast-paced world of logistics and e-commerce, a well-planned warehouse layout can make all the difference. From optimising workflow to ensuring safety compliance, the layout of your warehouse can significantly impact your operation’s efficiency and bottom line. This blog post aims to guide Logistics Managers and E-commerce Entrepreneurs through the intricacies of designing a warehouse layout that maximises productivity and minimises costs.
What is a Warehouse Layout?
Think of a warehouse layout as a well-organised puzzle of storage spaces, equipment, and pathways. The goal? To make everything run smoothly, cut down on waste, and boost efficiency. It’s all about ensuring goods move seamlessly from the moment they arrive to when they’re shipped out.
Key Elements of an Effective Warehouse Layout
When setting up your warehouse for your ecommerce business, there are a few elements that should take top priority. These core areas ensure your operations run efficiently from the start and set the foundation for future growth.
Receiving Area
This is where your products first arrive. A well-organized receiving area is essential for efficiently unloading, inspecting, and sorting goods. By streamlining this process, you can get products into your system faster, minimizing delays in order fulfilment.
Storage Area
Effective storage is key to organizing your inventory. Whether you use shelving, bins, or pallets, having a designated space for each product ensures your team can quickly locate items. Proper storage not only speeds up order picking but also reduces the risk of product damage.
Picking Area
The picking area is where your team collects items to fulfill orders. Organizing this space to prioritize high-demand products can significantly reduce picking times, allowing you to process orders faster and meet customer expectations for quick delivery.
Packing and Shipping Area
After picking, orders move to the packing and shipping area. This space needs to be equipped with packing materials, boxes, and shipping tools to prepare orders for dispatch. A streamlined packing process reduces shipping errors and ensures orders get to customers on time.
Additional Warehouse Elements to Consider as Your Needs Grow
As your ecommerce business expands, you may find it necessary to add more specialized areas to your warehouse. These additional elements can help you scale efficiently and further optimize your operations:
Replenishment Zones: Dedicated areas for restocking shelves to ensure high-demand products are always available for picking.
Return Processing Area: A specific space for handling returns, making it easier to inspect, restock, or dispose of returned items.
Cross-Docking Area: A system that allows fast-moving products to go straight from receiving to shipping, bypassing storage for quicker delivery.
Loading Dock: A well-organized area for loading trucks with outbound shipments, minimizing delays and keeping deliveries on track.
By focusing on the top four areas first, you can set a strong foundation for your warehouse operations. Then, as your needs grow, you can introduce these additional elements to further improve efficiency and scale your business.
How Warehouse Layouts Improve Your Business
Before diving into the specifics of setting up your warehouse, it’s important to understand why a well-designed layout is so crucial for your ecommerce business. The right warehouse setup isn’t just about organizing products—it’s a strategic asset that can significantly impact your efficiency, costs, and customer satisfaction. Here are the key benefits that highlight the importance of investing time and resources into your warehouse layout:
Faster Order Fulfillment
A well-organized warehouse layout allows for quick and efficient picking, packing, and shipping of orders. This reduces processing time and ensures customers receive their orders faster, which is critical for ecommerce businesses competing on delivery speed.
Maximized Storage Space
By optimizing storage solutions, such as using shelving, racks, or bins effectively, you can fit more inventory into the same square footage. This helps you store a larger variety of products without needing to expand your warehouse, saving costs.
Increased Accuracy
A clear, organized warehouse layout reduces the chances of errors during the picking and packing process. This ensures the right products are shipped to the right customers, lowering the risk of returns and boosting customer satisfaction.
Lower Operating Costs
Efficient workflows reduce unnecessary movement and time spent searching for products, which in turn lowers labor costs. A well-designed warehouse layout helps you run more cost-efficient operations by streamlining tasks.
Scalability
A flexible warehouse layout can easily adapt as your business grows. As order volumes increase, the layout can accommodate higher demand without needing a complete overhaul, making scaling smooth and less disruptive.
Better Inventory Management
A structured layout makes it easier to track and manage inventory, ensuring that stock levels are accurate and up-to-date. This helps prevent stockouts or overstocking, allowing you to efficiently meet customer demand while minimizing excess inventory.
Types of Warehouse Layout
Exploring different layouts can really help you maximize space and boost productivity. Each one comes with its own perks and challenges, so it’s key to pick one that aligns with your business goals. Let’s dive into some common warehouse layouts, weighing their pros and cons to find the best fit for your needs. Whether you’re aiming for speed, accuracy, cost-efficiency, or scalability, choosing the right layout is crucial for success.
U-shaped Layout
The U-shaped layout is one of the most popular designs due to its efficiency and ease of use. In this layout, goods are received on one side, stored in the middle, and shipped from the opposite side. This flow minimizes cross-traffic and streamlines operations.
Pros:
- Efficient flow of goods from receiving to shipping with minimal cross-traffic.
- Maximizes use of space in the middle for storage, making it easier to organize and manage inventory.
- Reduces the distance traveled by workers, improving operational efficiency.
Cons:
- Requires more space compared to other layouts, which may not be feasible for smaller warehouses.
- Could become inefficient for businesses that frequently handle high volumes of goods with rapid turnover.
Appropriate Application:
The U-shaped layout is best suited for large, high-volume operations that handle diverse product types. It’s ideal for warehouses with enough square footage to accommodate this layout while aiming for efficiency in the flow of goods.
L-shaped Layout
The L-shaped layout is ideal for warehouses with limited space. It allows for a logical flow of goods from receiving to storage to shipping, often using less square footage than other designs. This layout is particularly useful for smaller operations or those with irregularly shaped buildings.
Pros:
- Maximizes use of irregular or limited space, making it a good choice for smaller warehouses.
- Provides a clear flow of goods, which can reduce confusion and streamline operations in space-constrained areas.
- Efficient for smaller operations where high volumes of goods are not typically processed.
Cons:
- May not scale well for operations that require handling larger volumes of goods.
- Can result in congestion in the receiving and shipping areas if not properly managed, limiting workflow efficiency.
Appropriate Application:
L-shaped layouts are well-suited for smaller warehouses or those located in irregularly shaped buildings. This layout works best for businesses with lower volumes or limited space but still requires a clear, logical flow from receiving to shipping.
I-shaped Layout
The I-shaped layout features a straightforward, linear flow of goods from receiving to shipping. This design is particularly effective for operations that handle high volumes of goods with minimal variation in product types. It allows for easy scalability and straightforward management.
Pros:
- Simple, linear flow makes it easy to manage and scale for larger operations.
- Efficient for high-volume operations that process similar product types.
- Reduces worker movement, as goods flow directly from receiving to shipping without interruptions.
Cons:
- Can lead to congestion if traffic between receiving and shipping is not properly managed, especially in high-volume operations.
- Limited flexibility in managing varying product types or workflows, making it less ideal for businesses with diverse inventory.
Appropriate Application:
The I-shaped layout is ideal for high-volume operations that process uniform products, such as ecommerce businesses with streamlined product lines. It’s also well-suited for businesses that anticipate growth and need a scalable warehouse solution.
Custom Layouts
While standard layouts offer many benefits, custom designs can be tailored to meet specific operational needs. Custom layouts take into account unique factors such as product type, business model, and available space, providing a bespoke solution that maximizes efficiency.
Pros:
- Tailored to fit specific operational requirements, optimizing the space for unique product types and workflows.
- Provides flexibility in layout design, allowing businesses to address any special considerations like handling large or irregularly shaped products.
- Can maximize efficiency by adapting the space to match the company’s exact needs.
Cons:
- Typically more complex and costly to design and implement compared to standard layouts.
- Requires in-depth planning and ongoing adjustments to ensure the layout continues to meet operational needs as the business evolves.
Appropriate Application:
Custom layouts are best suited for businesses with unique operational needs, such as those handling a wide range of product types, or warehouses located in irregular spaces. These layouts are ideal for ecommerce businesses with specialized requirements that cannot be met by traditional designs.
Best Practices for Warehouse Layout Design
Key Considerations for Layout Planning
Space Utilisation
Maximising space utilisation is crucial for an efficient warehouse. This involves strategic placement of storage racks, packing stations, and equipment to ensure that every square metre is used effectively. Consider vertical space as well, as it can significantly increase storage capacity.
Workflow Optimisation
Optimising workflow involves planning the layout to minimise unnecessary movement and handling of goods. This can be achieved by placing frequently accessed items near the picking and packing areas, and arranging storage zones logically based on product type and turnover rate.
Accessibility and Safety
Ensuring easy access to all areas of the warehouse is essential for smooth operations. Wide aisles, clear signage, and well-organised storage areas contribute to a safer and more efficient work environment. Regular safety audits and employee training can further enhance accessibility and safety.
Tips for Efficient Warehouse Layout
Prioritising High-Traffic Areas
High-traffic areas, such as receiving docks and packing stations, should be prioritised in your layout. Placing these areas near each other reduces travel time and increases throughput. Ensure these zones are spacious enough to handle peak activity periods without congestion.
Effective Use of Vertical Space
Vertical space is often underutilised in warehouses. Installing high shelving units and mezzanine floors can dramatically increase storage capacity without expanding the warehouse footprint. Ensure that proper safety measures are in place when utilising vertical space.
Implementing Flexible Design Elements
Flexibility is key to future-proofing your warehouse layout. Modular shelving, movable workstations, and adjustable racking systems allow for easy reconfiguration as operational needs change. This adaptability can save time and money in the long run.
Components of a Warehouse LayoutSetup
Mapping Your Warehouse Space
Creating a Detailed Floor Plan
A detailed floor plan is the foundation of any successful warehouse layout. Use software tools to create accurate blueprints that include all key elements, such as storage areas, workstations, and pathways. This visual representation helps in identifying potential issues and planning efficient workflows.
Identifying Critical Zones
Critical zones include receiving and shipping areas, storage sections, and packing stations. Clearly defining these zones in your floor plan ensures that each area is optimised for its specific function. This clarity helps in preventing bottlenecks and improving overall efficiency.
Equipment and Space Requirements
Pallets and Shelving
Selecting the right pallets and shelving is crucial for effective storage. Consider the size, weight, and type of products you handle to choose appropriate storage solutions. Investing in high-quality shelving and pallets can prevent damage to goods and improve safety.
Material Handling Equipment
Material handling equipment, such as forklifts, pallet jacks, and conveyor systems, plays a vital role in warehouse operations. Ensure that your layout accommodates the movement and storage of this equipment. Regular maintenance and training can further enhance efficiency and safety.
Staffing Needs for Warehouse Layout
Determining Staffing Levels
Determining the right staffing levels is essential for smooth operations. Conduct a thorough analysis of your workflow to identify peak activity periods and allocate staff accordingly. This ensures that you have enough personnel to handle high volumes without overstaffing during slower periods.
Allocating Roles and Responsibilities
Clearly defined roles and responsibilities improve accountability and efficiency. Create job descriptions that outline specific tasks and expectations for each position. Regular training and performance evaluations can help in maintaining high standards and identifying areas for improvement.
Steps to Plan Warehouse Layout
Initial Assessment
Conducting a Space Audit
A space audit helps in understanding the current utilisation of your warehouse space. Identify areas that are underused or inefficiently organised. This assessment provides a baseline for planning improvements and optimising layout.
Understanding Operational Requirements
Understanding your operational requirements is crucial for designing an effective layout. Consider factors such as the volume of goods handled, the types of products stored, and the workflow processes. This information guides your layout planning and ensures that it meets your specific needs.
Designing the Layout
Drafting Preliminary Sketches
Drafting preliminary sketches allows you to experiment with different layout options. Use these sketches to visualise the placement of key elements and identify potential issues. This iterative process helps in refining your layout before finalising it.
Using Layout Planning Software
Layout planning software provides advanced tools for creating detailed and accurate floor plans. These tools offer features such as 3D visualisation, drag-and-drop functionality, and real-time collaboration. Using software can streamline the design process and improve accuracy.
Implementation and Testing
Setting Up the Warehouse
Once your layout is finalised, it’s time to set up the warehouse. This involves installing shelving, arranging equipment, and marking pathways. Ensure that all elements are placed according to the floor plan and that safety measures are in place.
Running Pilot Tests and Gathering Feedback
Running pilot tests helps in identifying any issues with the new layout before full implementation. Gather feedback from employees and address any concerns. This iterative process ensures that your layout is optimised for efficiency and safety.
Optimising Workflow in Warehouses
Enhancing Accessibility in Warehouses
Clear Signage and Labeling
Clear signage and labeling improve navigation and reduce errors. Use large, readable signs to mark key areas and pathways. Label storage racks and bins with detailed information to help employees quickly locate items.
Strategic Placement of Goods
Strategically placing goods based on their turnover rate improves efficiency. Frequently accessed items should be placed near picking and packing areas, while less frequently accessed items can be stored further away. This reduces travel time and speeds up order fulfilment.
Streamlining the Shipping Process
Efficient Loading and Unloading Areas
Efficient loading and unloading areas are crucial for smooth operations. Design these areas to accommodate multiple vehicles and ensure that there is sufficient space for manoeuvring. Clear pathways and proper lighting further enhance safety and efficiency.
Integrating Technology for Faster Processing
Integrating technology, such as barcode scanners and RFID systems, can significantly speed up the shipping process. These tools automate data collection and reduce manual errors, improving accuracy and efficiency.
Improving Picking Processes
Organising Inventory for Easy Access
Organising inventory for easy access improves picking efficiency. Use methods such as ABC analysis to categorise items based on their importance and turnover rate. This helps in prioritising high-value and frequently accessed items.
Utilising Automated Picking Systems
Automated picking systems, such as conveyor belts and robotic pickers, can further enhance efficiency. These systems reduce the reliance on manual labour and speed up the picking process. Regular maintenance and employee training are essential for optimal performance.
Overcoming Challenges in Warehouse Layout Design
Designing an efficient warehouse layout isn’t without its hurdles. For ecommerce businesses, these challenges can disrupt order fulfillment, create bottlenecks, or limit growth. But with the right strategies, these issues can be overcome. Let’s explore some of the most common challenges and practical solutions to keep your warehouse running smoothly.
Dealing with Space Constraints
Space is always a premium in warehouses, especially for growing ecommerce businesses. When inventory grows faster than your space can handle, things can quickly get cramped, affecting productivity and order fulfillment.
Smart Solutions:
- Think Up, Not Out: Maximize vertical space by using high-density storage like pallet racking and tall shelving. This lets you fit more inventory into the same square footage.
- Modular Shelving: Use movable or adjustable shelving that can be reconfigured as your needs change.
- Off-site Storage: For slower-moving or seasonal items, consider using off-site or third-party storage to free up space for fast-selling products.
Pro Tip:
Regularly audit your warehouse layout to spot underutilized areas. By making a few tweaks, you can free up valuable space and keep operations running smoothly without expanding.
Managing Seasonal Fluctuations
Seasonal sales spikes—think Black Friday or holiday shopping—can overwhelm your warehouse if you’re not prepared. During peak times, you may face increased demand for storage, staff, and space.
Smart Solutions:
- Flexible Layouts: Use movable shelving and reconfigurable zones to create extra space during peak seasons.
- Temporary Space and Staffing: Bring in temporary staff and allocate additional storage or packing areas to handle the surge in orders.
- Forecast Demand: Use demand forecasting tools to anticipate which products will spike and plan your inventory and space accordingly.
Pro Tip:
Prepare for busy seasons early. Stockpile fast-moving items and hire temporary staff well in advance to avoid last-minute chaos.
Maintaining Efficiency with High SKU Volumes
Handling a wide variety of products (SKUs) can lead to confusion, inefficiency, and longer picking times. When you’re juggling hundreds or thousands of SKUs, staying organized is crucial.
Smart Solutions:
- Slotting Optimization: Regularly review the placement of your products and store high-demand items in easily accessible locations to speed up picking.
- ABC Analysis: Categorize products into A (high demand), B (medium demand), and C (low demand), and store them accordingly. Keep high-demand items closest to the picking area.
- Technology: Use warehouse management systems (WMS), barcoding, or RFID technology to track and locate items quickly.
Pro Tip:
Reorganize your layout periodically based on sales data. As product popularity shifts, moving top sellers to more convenient locations can save time and reduce worker fatigue.
Ensuring Smooth Order Fulfillment During Growth
Growth is great, but it comes with its own challenges. As your ecommerce business expands, your warehouse operations may struggle to keep up. Without a scalable layout, you may experience fulfillment delays, mistakes, and operational inefficiencies.
Smart Solutions:
- Design for Scalability: Use scalable storage solutions like pallet racks or mezzanines, so your warehouse can grow without needing a major redesign.
- Automation: Automate repetitive tasks like sorting and packing with conveyors or robotic systems to keep up with increased order volumes.
- Optimize Workflow: Regularly evaluate your warehouse’s workflow to ensure that receiving, storage, picking, and shipping areas are efficiently connected.
Pro Tip:
Future-proof your warehouse by designing a layout that allows for incremental expansion. This ensures your warehouse can adapt to growth without disrupting your current operations.
Managing Returns Effectively
Returns are inevitable in ecommerce, especially in industries like fashion or electronics. A poorly managed returns process can slow down your warehouse operations and increase costs.
Smart Solutions:
- Dedicated Returns Area: Set aside a specific area for returns so they don’t disrupt regular operations.
- Streamlined Process: Use technology to automate the returns process, enabling faster inspection, sorting, and restocking of returned products.
- Returns Forecasting: Just like with inventory, use data to forecast return volumes so you can prepare staff and space during busy periods.
Pro Tip:
Encourage customers to make fewer unnecessary returns by providing accurate product descriptions, sizing guides, and images. This not only helps manage returns but also improves customer satisfaction.
Safety Regulations for Warehouses
Compliance with OSHA Standards
Compliance with OSHA standards is essential for a safe warehouse environment. Regular audits and inspections help in identifying and addressing safety issues. Provide ongoing training to employees to ensure that they are aware of safety protocols.
Regular Safety Audits and Training
Regular safety audits and training are crucial for maintaining a safe work environment. Conduct audits to identify potential hazards and implement corrective measures. Provide training to employees on safety procedures and emergency response.
Conclusion
A well-designed warehouse layout is critical for the success of any logistics or e-commerce operation. By understanding the key elements, types, and best practices for warehouse design, you can create a layout that maximises efficiency, reduces costs, and ensures safety.
Remember, the layout is not a one-time project but an ongoing process that requires regular assessment and optimisation. For further guidance, consider consulting with experts or using advanced layout planning software. Your warehouse has the potential to become a well-oiled machine, driving your business towards greater profitability and success.
If you feel that your business requires an expert approach to your warehouse layout and design, EIZ technology have over 20 years experience within the warehousing sector and we are more than happy to discuss this with your team. Feel free to book a call with us today!