Essential Tips for Successfully Managing a Warehouse [Ecommerce Edition]
23 Oct 2024
|by diadmin
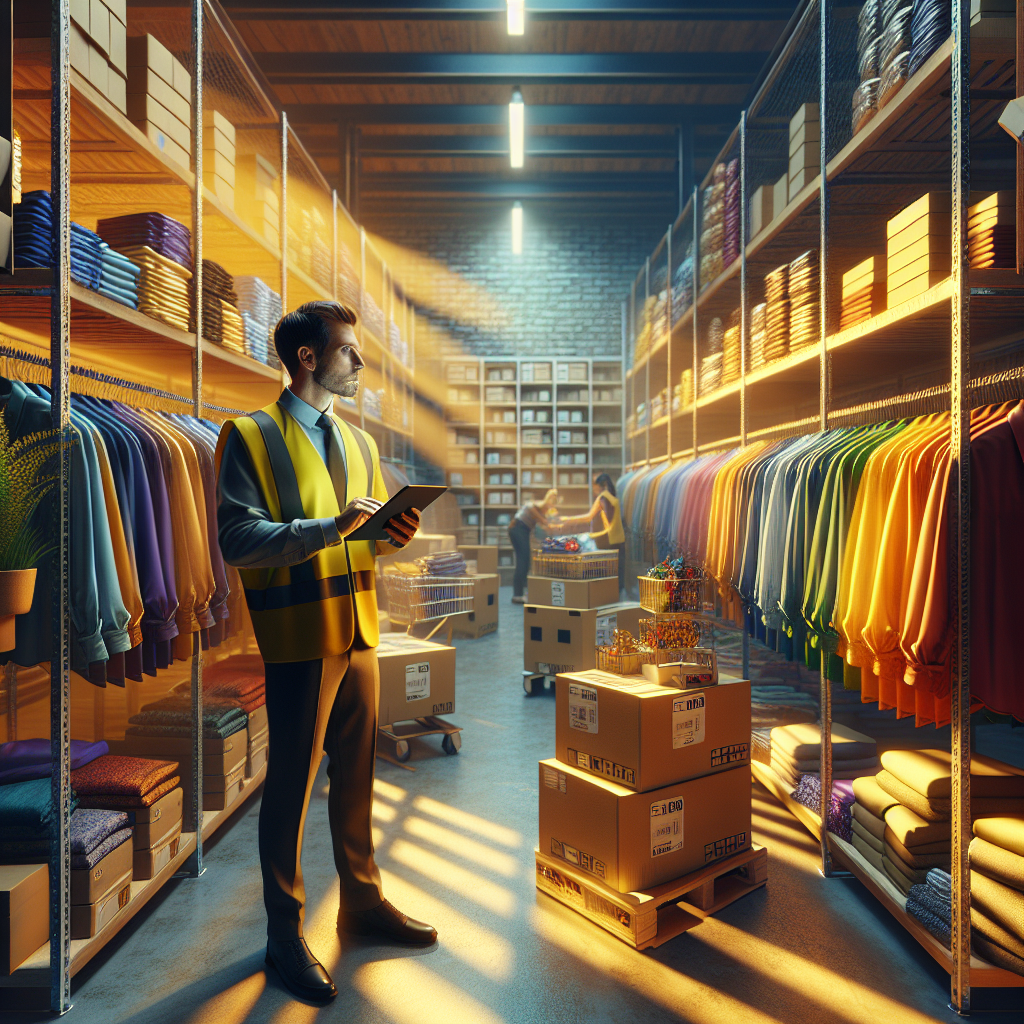
Managing a warehouse is no easy feat. It involves juggling countless tasks, from inventory management to employee scheduling, all while ensuring everything runs smoothly.
Without effective strategies, inefficiencies can pile up, leading to chaos and potential losses. A lack of organisation can overwhelm even the most experienced managers, causing disruptions that affect the entire supply chain.
Fortunately, mastering warehouse management is achievable with the right approach. By understanding the core principles of warehouse management, you can implement strategies that enhance organisation, efficiency, and attention to detail. Integrating an ecommerce warehouse with eCommerce platforms is crucial for streamlining fulfillment and minimizing errors.
Before we jump into our essential tips for successful warehouse management, let’s go over some ground rules for warehouse management and how it could benefit your ecommerce business.
What Is Warehouse Management?
Managing a Warehouse is all about executing, monitoring, and optimizing the operations within a warehouse. It’s like being a symphony conductor, ensuring everything runs smoothly.
Think about it, a lot is happening in a business’s warehouse. It’s a busy place, from receiving and storing inventory to fulfilling orders and shipping them out. Someone’s got to keep an eye on all these activities to make sure everything’s in order. This is where warehouse management software plays a crucial role, streamlining operations, improving productivity, and providing real-time insights into inventory management.
The goal? Well, effective warehouse management seeks to cut costs, boost productivity, and keep errors to a minimum. It’s all about making the warehouse a well-oiled machine!
Why Is Warehouse Management Important?
Managing a Warehouse is crucial for ensuring that goods-based businesses run smoothly. Adopting good practices streamlines operations, boosts efficiency, and enhances customer experience with smoother workflows, fewer errors, and timely deliveries.
Satisfied customers lead to increased loyalty and positive reviews, driving repeat business and attracting new clients.
Efficient warehouse management significantly contributes to profitability. By optimizing inventory and reducing waste, businesses can lower costs and increase profit margins.
For companies looking to scale, robust warehouse management is essential. It provides the foundation to handle increased volumes without compromising quality or service. Effective warehouse management is not just a logistical necessity; it’s a strategic advantage in a competitive market. Integrating warehouse management with supply chain management systems enhances overall efficiency by optimizing product storage and improving operations in multi-location warehouses.
What Are The Most Common Warehouse Functions?
Managing a warehouse may appear simple, but optimizing warehouse processes involves a complex network of activities happening behind the scenes to ensure seamless operations. Whether you’re a veteran eCommerce entrepreneur or just embarking on your journey, grasping these fundamental functions can help you optimize your operations and enhance efficiency. Let’s explore the eight most common operational functions of a warehouse:
- Receiving
The process begins here. Receiving involves accepting incoming goods from suppliers, which is more than just unloading trucks. It’s about verifying that the correct products have arrived in the right quantities and in good condition. Efficient receiving helps catch mistakes early, preventing inventory inaccuracies later on.
- Put-Away
Once goods are received, they must be moved to their designated storage areas. Put-away involves transferring items from the receiving area to their rightful locations within the warehouse. Performing this task efficiently reduces handling time and simplifies product retrieval. Clear labeling and organized shelving can significantly improve this process.
- Storage
Storage goes beyond merely stacking products on shelves. It involves organizing inventory to maximize space and facilitate easy retrieval. This includes using vertical space, implementing intelligent shelving systems, and arranging products based on size, weight, and picking frequency.
- Inventory Management
Monitoring the contents of your warehouse is crucial. Inventory management includes tracking stock levels, product locations, and managing stock rotation. Effective inventory management prevents overstocking or stockouts, ensuring you have the right amount of product to meet demand without tying up excessive capital.
- Order Picking
When an order is placed, it’s time to pick the items from their storage locations. Efficient order picking is essential for quick turnaround. Methods such as batch picking, zone picking, or using pick-to-light systems can accelerate this process and minimize errors.
- Packing
After picking, items need to be packed for shipment. Packing involves choosing suitable packaging materials, protecting products from damage, and preparing them with shipping labels and documentation. Efficient packing ensures products arrive safely and keeps customers satisfied.
- Shipping
Shipping is the last step in delivering products to customers. This function includes scheduling carriers, loading goods onto delivery vehicles, and ensuring all shipping documentation is precise. Timely and efficient shipping is crucial for meeting delivery expectations and providing excellent customer service.
- Returns Processing (Reverse Logistics)
Returns are an inevitable aspect of eCommerce. Efficient returns processing involves receiving returned products, inspecting them, updating inventory records, and determining subsequent steps (restocking, disposal, or repair). Effectively handling returns can enhance customer satisfaction and help recover value from returned items.
Expert Tips For Managing a Warehouse
Efficient warehouse organisation is crucial for a seamless eCommerce operation. Here are some straightforward yet effective strategies to maintain flow and efficiency:
Plan for flow and involve your team:
Design your warehouse layout to ensure smooth flow, avoiding any backtracking during picking or packing. Warehouse managers play a critical role in designing the warehouse layout and involving the team to optimize operations. Clear pathways reduce walking time, and gathering feedback from your staff can highlight areas for improvement.
Establish zones and workstations:
Create specific zones for different types of picking—bulk orders, single items, etc.—and set up dedicated workstations for packing and shipping. This organisation speeds up processes and keeps everything orderly.
Organise for efficiency:
Position fast-moving, high-demand products at the front of aisles for easy access, and focus on organizing warehouse space to enhance efficiency. Keep the space tidy with stackable bins and clear labeling to help your team quickly locate items, reducing errors and saving time.
Eliminate clutter and allocate space for receiving:
Regularly declutter to keep operations smooth. Ensure there’s a designated receiving area for new stock to sort and inspect items before storage.
Optimize your shipping area:
Arrange your shipping station for efficiency—keep packing materials, tape, and labels within easy reach to expedite order dispatching.
Use stackable bins and label everything:
Stackable bins are a game-changer for small items and overflow stock, saving space and making it easier to find things. Label your shelves and bins so your team can quickly spot what they need, reducing mistakes and speeding things up.
Sort by order frequency:
Put high-demand products where they’re easy to grab. Slower-moving stock can be kept further away to keep the prime spots free for fast sellers.
By staying organised and thinking about flow, you’ll not only speed up your operations but also make life easier for your team.
Warehouse Layouts And How To Maximise Space
In a growing eCommerce business, space can be a valuable asset. Here’s how to maximize your available space:
- Optimize Space Utilisation: Reevaluate how you’re using your current space. Can you rearrange or shift items to store more inventory? Efficiently utilizing every corner can often free up more room than expected.
- Leverage Vertical Space: Don’t just focus on floor space—think vertically! Install taller shelving or racking to store items upward. You’ll be amazed at how much more stock can fit without requiring additional square footage.
- Upgrade and Reorganize Racking Systems: If your setup has been the same for a while, consider upgrading your racking systems. Adjustable shelving or high-density storage solutions can help you store more efficiently while keeping everything organized.
- Implement a Warehouse Management System (WMS): A WMS can optimize your layout by determining the best locations for each product based on order frequency, size, and other factors. It also streamlines picking paths and enhances overall efficiency, maximising your space usage.
By rethinking your layout and effectively utilising both horizontal and vertical space, you can store more inventory and maintain your warehouse’s peak efficiency.
Inventory Management Made Simple: Best Practices for Effective Inventory Management
Keeping your warehouse organised and running smoothly starts with smart inventory management. Here are some practical tips to help you make the most of your space, streamline picking, and stay on top of stock levels. Utilizing inventory management software can significantly streamline inventory processes and enhance accuracy.
Inventory Storage Strategies
- Organise for easy access: Arrange store inventory so it’s easy to find. Group similar items together and keep frequently picked products within easy reach.
- Use vertical space: Make use of your warehouse’s height by stacking items. This helps you store more without needing extra floor space.
- Leverage a WMS: A Warehouse Management System (WMS) can suggest the best storage spots for your items based on order frequency and size. This ensures efficient use of space and faster retrieval.
Inventory Tracking and Reporting
- Use a tracking system: Implement a system that gives you real-time updates on inventory levels and locations, helping you avoid over- or under-stocking.
- Generate reports with a WMS: An inventory management system can track stock movements, generate reports, and help you analyze trends so you can make better reordering decisions.
Inventory Classification
Organising inventory by value and sales frequency can make your warehouse more efficient. Here’s how to use ABC analysis:
- Category A: High-value items with lower sales frequency—store securely and monitor closely.
- Category B: Mid-range items with moderate sales—important but not top priority.
- Category C: Low-value, fast-selling items—keep these easily accessible for quick retrieval.
By applying these strategies, you’ll improve your storage, make inventory management easier, and create a more efficient warehouse.
Warehouse Operations
Streamlining Order Processing
In the fast-paced world of ecommerce, streamlining order processing is crucial for maintaining efficient warehouse operations. Implementing a robust warehouse management system (WMS) can automate a multitude of tasks, from order receipt to inventory allocation and shipping. This automation not only reduces errors but also significantly boosts productivity and enhances customer satisfaction.
A WMS can handle the complexities of order processing with ease, ensuring that each step is executed flawlessly. For instance, integrating a pick-to-light or pick-to-voice system can revolutionize the way your warehouse staff picks orders. These systems guide employees through the picking process with visual or auditory cues, ensuring quick and accurate order fulfilment. By leveraging these technologies, you can create a more efficient and error-free order processing workflow.
Efficient Picking, Packing, and Shipping
Efficient picking, packing, and shipping are the backbone of successful warehouse operations. Implementing a zone-picking system can drastically reduce travel time within the warehouse, allowing staff to focus on specific zones and pick orders more efficiently. This method not only increases productivity but also minimizes the chances of errors.
Automated packing machines are another game-changer. These machines can handle the packing process with precision, reducing labour costs and ensuring consistent packaging quality. By automating this step, you can free up your staff to focus on more value-added tasks.
Finally, integrating a shipping system that works seamlessly with carriers can streamline the shipping process. This integration ensures that shipping labels and documentation are accurate, reducing the risk of errors and delays. By optimizing your picking, packing, and shipping processes, you can enhance overall warehouse efficiency and improve customer satisfaction.
Warehouse Technology
Benefits of a Warehouse Management System (WMS)
A Warehouse Management System (WMS) is essential for businesses aiming to streamline warehouse operations and enhance efficiency. Warehouse management systems provide crucial tools for automating processes, offering real-time data visibility, and managing inventory efficiently. Regardless of warehouse size, a WMS provides numerous benefits that simplify inventory and workflow management.
Key benefits include:
- Enhanced Inventory Accuracy: A WMS offers precise data on stock levels, preventing overstocking and stockouts, while making inventory audits quicker and more reliable.
- Accelerated Order Fulfillment: By optimizing stock locations and picking paths, a WMS expedites the order picking and packing process, reducing delivery times.
- Optimized Space Utilization: By recommending optimal storage locations, a WMS improves storage density and minimizes wasted space.
- Increased Productivity: Automated processes and real-time updates enable staff to focus on higher-value tasks, boosting operational efficiency.
- Seamless System Integration: A WMS integrates with other business software, such as ERP and shipping systems, facilitating smooth inter-departmental communication and reducing manual data entry.
Embracing Automation for Efficiency
Incorporating automation into your warehouse operations is key to achieving higher efficiency and accuracy. Automated storage and retrieval systems (AS/RS) can significantly reduce labor costs and improve inventory accuracy by automating the storage and retrieval of goods. These systems ensure that items are stored in optimal locations and retrieved quickly when needed.
Automated guided vehicles (AGVs) are another valuable addition to modern warehouses. These vehicles can transport goods throughout the warehouse without human intervention, reducing labor costs and enhancing safety. By implementing AGVs, you can streamline material handling and improve overall operational efficiency.
A warehouse control system (WCS) can further enhance your operations by providing real-time monitoring and control. This system allows you to oversee all warehouse activities, ensuring that everything runs smoothly and efficiently. By embracing automation, you can create a more efficient, accurate, and safe warehouse environment.
Why Partnering With Lofko Is The Right Choice For Your Business
Managing a warehouse? Lofko’s Warehouse Management System (WMS) equips you with complete operational control. From real-time inventory tracking to minimising picking and packing errors, Lofko enhances efficiency and scales seamlessly with your business growth.
With Lofko WMS, automate key tasks, optimize space, and monitor your warehouse’s performance directly from your phone or tablet. Whether managing a single or multiple locations, Lofko ensures smooth operations, faster fulfillment, and improved inventory control.
Ready to advance? Utilise Lofko’s integration features to expand into new markets, reduce shipping costs, and expedite international deliveries with ease. To see how our platform can empower your business, you can book a free strategy call with our team today. Click here
Warehouse Safety and Security Tips
Cultivating a Safety Culture and Upholding Guidelines
Establishing a robust safety culture involves prioritizing safety and ensuring that all team members adhere to established protocols. Here’s how to nurture a safe warehouse environment:
Engage Employees Through Training
Involve your team in discussions about potential hazards, safety practices, and the correct usage of personal protective equipment (PPE). Providing regular and ongoing training helps reinforce proper procedures and ensures consistent compliance.
Encourage Reporting and Conduct Audits
A strong safety culture encourages employees to feel at ease reporting incidents or concerns. Regular audits of your warehouse’s facilities, equipment, and layout help identify potential hazards and ensure compliance with standards.
Securing the Warehouse Environment
Warehouse security is equally crucial for safeguarding products and ensuring seamless operations:
Implement Security Measures
Utilize security cameras, locks, and access control systems to maintain a secure warehouse environment.
Leverage a Warehouse Management System (WMS)
A Warehouse Management System not only tracks inventory but also monitors warehouse activities. This adds an additional layer of security, effectively managing both safety and security.
Warehouse Staffing and Training
Hiring and training warehouse staff is essential for ensuring safety and efficiency in operations. Here’s how to prepare and motivate your team effectively:
Employee Hiring and Training
Given the potential hazards of warehouse work, proper training is crucial. Educate employees on safety protocols and the correct use of equipment. Regular training sessions and opportunities for skill enhancement not only keep your team safe but also ensure seamless operations.
Continuous Development and Safety Enhancements
Ongoing training is key to maintaining employee efficiency and safety. Encourage staff to report any incidents or near-misses to enhance safety practices. Implementing a Warehouse Management System (WMS) can help monitor performance and deliver timely feedback.
Evaluating and Motivating Employee Performance
Set Clear Benchmarks and Incentivize Performance
Establish straightforward performance benchmarks to motivate employees and drive continuous improvement. Consider using reward systems or incentive-based pay structures to boost productivity.
Conduct Regular Performance Reviews
Regularly evaluate employee performance to ensure compliance with safety and efficiency standards. Offer constructive feedback to keep them aligned with organizational goals.
Integrating Warehouse Management with Ecommerce
Aligning Warehouse Practices with Online Sales
For ecommerce businesses, aligning warehouse practices with online sales is essential for success. Implementing a warehouse management system (WMS) that integrates seamlessly with ecommerce platforms can streamline order processing and enhance customer satisfaction. This integration ensures that orders are processed quickly and accurately, reducing the risk of errors and delays.
Real-time inventory management is another critical component. By keeping track of inventory levels in real-time, you can prevent stockouts and overstocking, ensuring that you always have the right amount of product on hand. This not only improves customer satisfaction but also optimizes your inventory investment.
Additionally, integrating a shipping system that works with carriers can streamline the shipping process. This integration ensures that shipping labels and documentation are accurate, reducing the risk of errors and delays. By aligning your warehouse practices with online sales, you can create a more efficient and customer-centric operation, driving growth and success in the competitive ecommerce market.
Tips for Quality Control and Inspection
Quality control is critical for businesses of all sizes, helping to build a strong brand, boost sales, and foster customer loyalty. Implementing proper procedures ensures that your products consistently meet high standards, which is key to long-term success. Regular inspections focused on cleanliness, safety, equipment, and inventory are essential for keeping the warehouse efficient. A Warehouse Management System (WMS) can be invaluable for tracking inventory, monitoring warehouse activity, and addressing any quality issues quickly. By staying on top of quality control, you can deliver reliable products that strengthen your reputation and maintain customer trust.
Key Tips:
- Conduct regular inspections for cleanliness, safety, and equipment condition.
- Use a WMS to track inventory and monitor warehouse performance.
- Quickly evaluate and address quality issues to maintain product consistency.
- Implement strong quality control procedures to ensure high standards are met.
Best Practices for Warehouse Management
Unlock the full potential of your warehouse with these expert tips and strategies. Whether you’re looking to streamline operations, enhance efficiency, or slash costs, here’s how you can elevate your warehouse management game:
Evaluating Meaningful KPIs
Imagine having a dashboard that tells you exactly how well your warehouse is performing at a glance. That’s the power of Key Performance Indicators (KPIs). Here’s how to make them work for you:
Track the Right Metrics
Focus on vital signs like order accuracy, inventory turnover, and delivery times. These metrics are the pulse of your warehouse’s health.
Harness Your Tech
Use a Warehouse Management System (WMS) to keep an eye on these metrics in real-time. It’s like having a fitness tracker for your warehouse!
Keep Tabs and Adapt
Regularly check your KPIs to stay agile and responsive. It’s all about making smart adjustments on the fly to keep operations smooth and efficient.
Practicing Continuous Improvement
Think of your warehouse as a pro athlete. There’s always room for a little more fine-tuning:
- Iterative Enhancements: Small tweaks can lead to big gains. Continuously refine your processes to cut waste and ramp up efficiency.
- Insist on Quality: Set up strict quality control checkpoints. Because when it comes to customer satisfaction, every detail counts.
- Leverage the Latest Tech: Keep your operations cutting-edge with the latest WMS tech. It’s like upgrading your warehouse to a smarter, faster version of itself.
Addressing Common Warehouse Management Challenges
Every warehouse faces its set of challenges, but here’s how you can tackle them head-on:
- Spot Issues Early: Stay proactive and resolve problems like inventory mismatches or shipping delays before they escalate.
- Implement Smart Solutions: Use your WMS to streamline and enhance every aspect of your operations.
- Build Resilience: Develop strategies to not just solve, but prevent common issues. It’s about building a warehouse that’s not only efficient today but robust for tomorrow.
By integrating these best practices into your warehouse management, you’ll not only boost your operational efficiency but also create a dynamic workplace that’s ready to meet the demands of tomorrow. Let’s make your warehouse work smarter, not harder! Contact Us Today!