Mastering the Pick to Pack Process: A Comprehensive Guide For Ecommerce
23 Dec 2024
|by diadmin
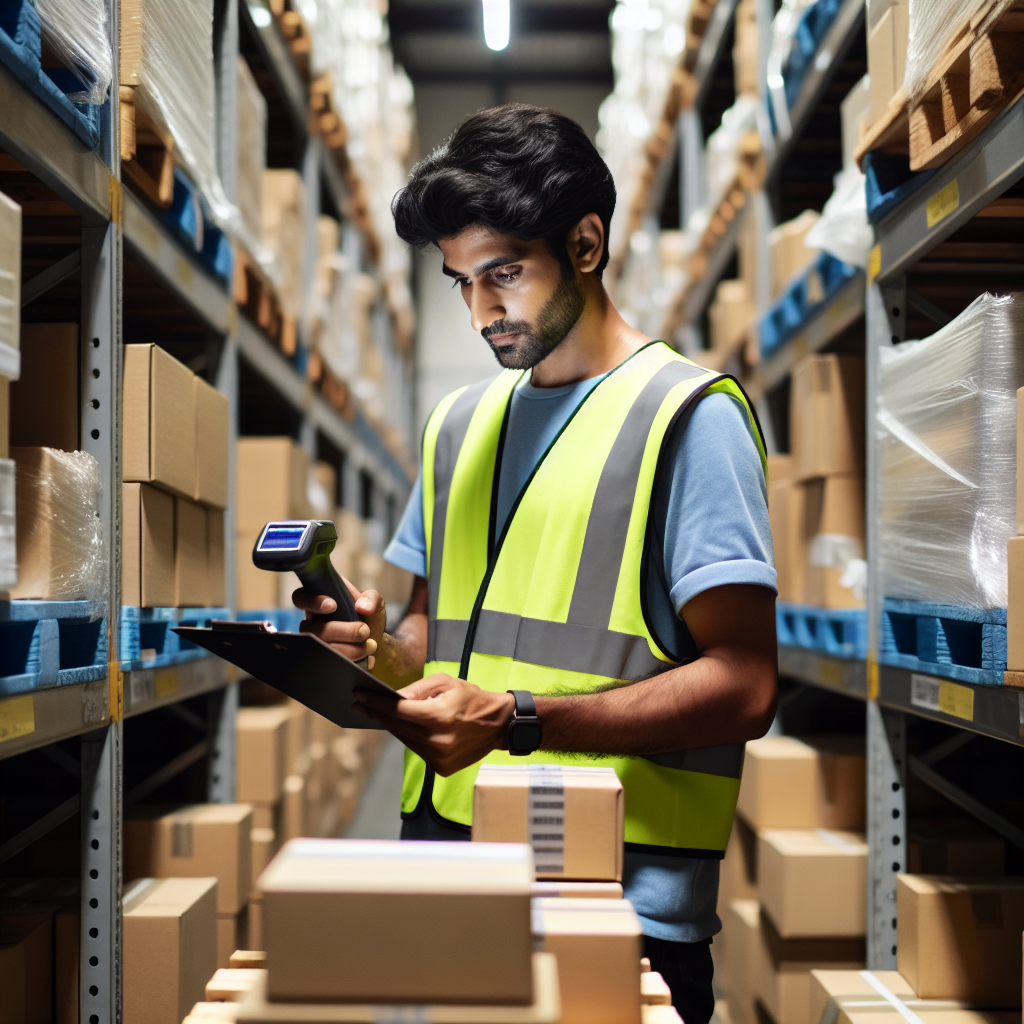
Struggling to keep your ecommerce orders accurate and on time? An inefficient pick and pack process could be holding your business back, leading to delayed deliveries, unhappy customers, and missed sales. When your warehouse operations are disorganised, and staff are scrambling to find products, every second counts and it’s costing you.
The good news? With the right strategies and tools, you can streamline your pick and pack services, saving time, reducing costs, and improving customer satisfaction. In this guide, we’ll show you how to optimise every step of your fulfilment process and turn it into a powerful advantage for your business.
Understanding the Pick and Pack Process
The pick and pack process is crucial in e-commerce order fulfillment. It involves creating a picking list, selecting products, packing them, and preparing them for shipping, ensuring customers receive their orders accurately and efficiently.
In the fast-paced e-commerce world, pick and pack is the backbone of fulfillment operations. It begins with generating a picking list, guiding warehouse staff to collect items for each order. After picking, products move to the packing station, where they are carefully packaged to ensure safe delivery. Finally, the packed orders are prepped for shipping.
The pick and pack process significantly impacts delivery speed, order accuracy, and customer satisfaction. A streamlined process ensures prompt and correct deliveries, builds trust and loyalty, and encourages repeat business. Mastering this process is key to staying competitive in the e-commerce market.
Order Receiving and Verification
When orders come in through your ecommerce store, they’re verified for accuracy before being sent to your warehouse management system (WMS). This software generates a picking list, guiding your warehouse pickers in the warehouse picking process to locate products quickly and efficiently. The WMS takes the guesswork out of finding items, reducing errors and saving valuable time.
Product Picking
This is where the action happens. Warehouse workers follow the picking list using strategies like piece picking, batch picking, zone picking, or wave picking. Each method has its own benefits (we will discuss in more detail below), but the goal is the same: to pick products in the most efficient route possible, minimising walking distances and ensuring accuracy. Whether you choose batch picking to manage multiple orders at once or zone picking for more organised warehouse setups, the right strategy makes a big difference in speed and accuracy.
Order Packing
After picking, the next step is the packing process. This involves using appropriate packing materials to secure the items, printing the shipping label, and making sure everything is set for delivery. A well-organised packing station with all the right tools can speed up this step, ensuring that every order is packaged neatly, meets customer expectations, and even includes branded packaging if you want to leave a lasting impression.
Shipping
Finally, packed orders are sent out for delivery. With everything in place, from accurate picking to secure packing, you reduce the risk of shipping errors, keeping your customers happy and building a reliable reputation for your ecommerce business.
By mastering the pick and pack process, ecommerce businesses can keep warehouse operations running smoothly, minimise shipping costs, and manage fluctuating order volumes with ease. An efficient process means more than just getting orders out the door—it’s about consistently delighting customers, optimising costs, and driving growth for your business.
Order Picking Strategies
Choosing the right picking strategy is critical for scaling your operations efficiently. Here’s a breakdown of the most common strategies and when to use them.
Piece Picking
Perfect for smaller operations, this method involves picking one order at a time. It’s simple and straightforward but may not be the most efficient route for larger volumes.
Batch Picking
This strategy groups multiple orders together, allowing pickers to collect items for several orders in one go. It’s a time-saver when managing fluctuating order volumes and high sales periods.
Zone Picking
This method assigns warehouse pickers to specific zones within the warehouse space, where they focus on picking items only from their designated area. This works well for larger facilities and helps minimise walking distances.
Wave Picking
Ideal for busy ecommerce stores, wave picking allows your team to pick items across multiple zones simultaneously, making the most of your warehouse’s capacity during peak periods.
Warehouse Setup for Efficient Pick and Pack
An efficient warehouse setup is the foundation of a smooth pick and pack process. Whether you’re managing an expanding ecommerce business or fine-tuning your existing operations, optimising your warehouse space can lead to quicker fulfilment, reduced costs, and happier customers. Let’s explore how to set up your warehouse for success.
Inventory Management Strategies
Effective inventory management is crucial for ensuring that products are easy to locate, pick, and pack, with warehouse picking playing a vital role in this process. Different strategies work for different businesses, but here are a few proven methods:
- Chaotic Inventory Management: This approach involves storing products randomly in the available shelving space. While it might sound unorganised, it actually allows for efficient use of warehouse space. The key is using a warehouse management system (WMS) to track exactly where every item is located.
- Volume Inventory Management: This strategy focuses on storing the highest-selling products closest to the packing station. By positioning high-demand items within easy reach, you can reduce picking times significantly and boost the overall speed of your pack fulfilment process.
- Class-Based Inventory Management: This method groups products into categories or classes, such as bestsellers, seasonal items, or fragile products. By organising your warehouse based on these categories, you make it easier for warehouse workers to locate and pick items, improving efficiency and accuracy.
Choosing the right inventory management strategy is all about understanding your business needs and sales patterns. The right approach helps reduce errors and ensures your team can find products quickly, meeting customer expectations for fast shipping.
With a solid inventory management strategy in place, the next step is to optimise your warehouse layout to maximise efficiency.
Optimising Warehouse Layout and Design
The layout and design of your warehouse directly impact how efficient your pick and pack process will be. A well-designed warehouse should minimise walking distances for pickers, make the best use of storage capacity, and streamline your packing and shipping processes.
- Strategic Product Placement: Place popular and frequently ordered products near packing stations and shipping areas. This reduces the time it takes for warehouse pickers to collect items and move orders through the pack process.
- Clear Pathways and Labelling: Ensure all pathways are wide enough for easy movement of people and warehouse machinery. Labelling shelves and aisles clearly can also guide pack workers efficiently, reducing delays and confusion.
- Flexibility for Fluctuating Order Volumes: As order volumes can fluctuate, especially during peak seasons or sales events, your warehouse setup should be adaptable. Using adjustable shelving and modular storage units allows you to reconfigure your warehouse space quickly, so you can scale your pack operations as needed.
By focusing on optimising your warehouse layout and choosing the right inventory management strategy, your business can enhance efficiency, reduce picking times, and keep your pack operations running smoothly. This not only saves time and money but also ensures that your customers receive their orders promptly and accurately.
Technology and Software for Pick and Pack
Integrating technology like a warehouse management system (WMS) is essential for optimising your pick and pack operations. A robust WMS like Lofko not only manages inventory but also includes built-in pick and pack software that enhances efficiency in every stage of the fulfilment process. By automating tasks such as generating picking lists, tracking real-time inventory, and coordinating shipping processes, Lofko streamlines the entire workflow.
Lofko’s All-in-One Solution
Lofko’s WMS is more than just inventory management; it offers a comprehensive pick and pack system that manages everything from picking routes to packaging and shipping. This integration ensures that ecommerce businesses don’t need to rely on multiple systems for different aspects of their warehouse operations.
Here’s how Lofko’s pick and pack functionality optimises the pack fulfilment process:
- Improved Picking Efficiency: The system supports multiple picking strategies like batch picking, wave picking, zone picking, and piece picking, helping your warehouse workers locate products using the most efficient routes. This reduces walking distances and turnaround times, increasing overall productivity.
- Integrated Packing Operations: Lofko’s software assists in managing the packing process, ensuring that packing stations are fully equipped with the right tools, from packing slips to shipping labels. It also guides staff on using appropriate packing materials to secure items, minimising errors and enhancing the unboxing experience for customers.
- Real-Time Data and Performance Tracking: With built-in tracking mechanisms, Lofko allows businesses to monitor key metrics such as picking accuracy, fulfilment costs, and warehouse performance. This data helps identify bottlenecks and optimise operations continuously, ensuring the business can meet fluctuating order volumes efficiently.
By using an all-in-one solution like Lofko, ecommerce businesses can enhance their pick and pack processes, ensuring cost savings, reduced errors, and better management of their warehouse space. This integrated approach not only supports scaling operations but also guarantees that the business delivers a consistent, high-quality customer experience.
Managing Costs and Fees
Managing costs and fees is crucial for e-commerce businesses to maintain profitability. The pick and pack process can be a significant contributor to costs, and understanding the pick and pack fee is essential for optimizing costs.
In the realm of e-commerce, every penny counts. The pick and pack process, while essential, can also be a significant cost driver. From labor costs associated with picking and packing to the expenses of packing materials and shipping, these fees can add up quickly. Therefore, understanding and managing these costs is vital for maintaining healthy profit margins.
Understanding the Pick and Pack Fee
The pick and pack fee is the cost of picking each product and packing it for shipping. This fee can vary depending on the type of product, the weight and size of the product, and the shipping destination. Understanding the pick and pack fee is essential for e-commerce businesses to optimize their costs and ensure that they are charging their customers the correct amount.
The pick and pack fee encompasses several elements. It includes the labor cost of picking each item from the warehouse shelves, the cost of packing materials, and the time spent packing the items securely. Additionally, factors such as the weight and size of the product, as well as the shipping destination, can influence the fee. For instance, larger or heavier items may incur higher fees due to the increased effort and materials required to pack them.
By understanding these fees, e-commerce businesses can better manage their pricing strategies, ensuring they cover their costs while remaining competitive. It also allows businesses to identify areas where they can cut costs without compromising on service quality.
Cost-Saving Strategies
There are several cost-saving strategies that e-commerce businesses can implement to reduce their pick and pack fees. These include:
- Implementing a Warehouse Management System (WMS): A robust WMS can optimize warehouse operations, reducing labor costs by streamlining the picking and packing process. It ensures that inventory is accurately tracked, and picking routes are optimized, saving time and reducing errors.
- Using Batch Picking and Wave Picking: These methods allow pickers to collect items for multiple orders in one go, reducing the number of trips to the warehouse shelves and increasing efficiency.
- Using Zone Picking: By assigning pickers to specific zones within the warehouse, businesses can reduce the distance that staff need to travel, speeding up the picking process.
- Using Appropriate Packing Materials: Selecting the right packing materials can reduce packaging costs and ensure products are protected during transit, minimizing the risk of returns.
- Implementing a Pack Fulfillment Process: Streamlining the pack fulfillment process can minimize the number of packages and reduce shipping costs. This includes consolidating orders where possible and using efficient packing techniques.
By adopting these strategies, e-commerce businesses can significantly reduce their pick and pack fees, improving their bottom line while maintaining high standards of service.
Best Practices for Efficient Pick and Pack
Mastering the pick and pack process is about more than just getting orders out the door—it’s about doing it efficiently, accurately, and in a way that delights your customers. By following a few best practices, your ecommerce business can optimise fulfilment operations, reduce costs, and exceed customer expectations. Let’s explore some key strategies.
Order Packing Best Practices
Packing orders might seem straightforward, but there are effective ways to streamline this process while maintaining high standards. A well-organised packing station and the right packing materials can make all the difference:
Use the Right-Sized Packaging
Always match packaging size to the items being shipped. Many couriers, including those in Australia, calculate shipping costs based on the greater of the dead weight (actual weight) or cubic weight (volume of the package). If your package dimensions are larger than necessary, you may incur higher cubic weight charges even if the actual weight is low. By optimising the size of your packages, you can minimise shipping costs, as couriers typically prefer dead weight charges over cubic weight charges.
Protect Items Properly
Using appropriate packing materials like bubble wrap, packing peanuts, or air pillows ensures that items arrive safely. It’s essential to balance protection with efficiency—using too much material can be wasteful, while too little can risk product damage. Properly packed items reduce the risk of returns and enhance customer satisfaction.
Organise Your Packing Station
Keep your packing station stocked with necessary materials and equipment, like tape dispensers, packing slips, and shipping labels. A tidy and organised space allows pack workers to operate efficiently, reducing time spent on each order and ensuring that orders are packed accurately and securely.
By implementing these best practices, businesses can improve their pack processes, cut down on shipping costs, and enhance customer satisfaction, leading to more positive reviews and repeat business.
Kitting and Bundling
Kitting and bundling is a strategy where multiple products are packaged together as a single unit. This can streamline your pick and pack process, especially for products that are frequently purchased together. Here’s how it can benefit your business:
- Improved Efficiency: By pre-packing kits of products that are commonly ordered together, you can reduce the time and labour needed to fulfil these orders, speeding up the overall fulfilment process.
- Cost Savings: Bundling products can help save on packaging materials and shipping costs, as you can consolidate items into a single package rather than shipping them separately.
- Enhanced Customer Experience: Offering product bundles can also increase sales by providing customers with convenient options and value-for-money deals, making their shopping experience more satisfying.
By leveraging kitting and bundling, you not only optimise your pack system but also create new opportunities to increase sales and build customer loyalty.
Challenges and Solutions
Even with the best systems and strategies in place, challenges in the pick and pack process are inevitable, especially for growing ecommerce businesses. Understanding these common hurdles and implementing effective solutions can help you maintain efficiency, minimise errors, and keep your customers satisfied. Let’s explore some key challenges and practical solutions.
Common Challenges in the Pick and Pack Process
- Inaccurate Inventory Management: When inventory levels are not accurately tracked, it can lead to stockouts, delays in order fulfilment, and disappointed customers. Without a reliable system in place, it’s challenging to manage fluctuating order volumes, particularly during peak sales periods.
- Higher Turnaround Times: Inefficiencies in the picking process, such as unorganised warehouse shelves or inefficient picking routes, can lead to higher turnaround times. This impacts how quickly orders are shipped, leading to potential customer dissatisfaction.
- Human Errors: Mistakes in picking and packing are common when processes rely heavily on manual work without adequate verification systems. Errors like picking the wrong item or incorrect packing can increase return rates and affect customer trust.
- Unavailability of Product Information: If your pack workers don’t have access to real-time product information or locations within the warehouse, it can cause delays and mistakes in the fulfilment process.
- Lack of Tracking Mechanisms: Without a system to track the status of orders through each stage of the pack fulfilment process, it’s difficult to identify bottlenecks or address issues quickly. This can lead to delays in shipping and poor customer experiences.
Solutions and Strategies for Improvement
- Implement a Robust Warehouse Management System (WMS): Solutions like Lofko offer an all-in-one approach to managing warehouse operations efficiently. A WMS provides real-time inventory tracking, optimised picking lists, and performance analytics, all of which help reduce errors and improve turnaround times. By using technology to automate key aspects of the pick and pack process, you minimise human error and keep orders flowing smoothly.
- Optimise Warehouse Layout and Design: Efficient warehouse setup is essential for minimising walking distances and improving the picking process. Strategies such as storing high-volume products close to packing stations or using clear labelling and pathways can significantly reduce the time it takes to fulfil orders.
- Automate the Pack Process: Automating elements of the pack process, like using automated packing machines or robotic picking systems, can help improve efficiency and reduce labour costs. These systems are particularly beneficial during peak periods when fluctuating order volumes can strain manual operations.
- Train and Incentivise Personnel: Training your warehouse team thoroughly and incentivising them for performance can improve accuracy and speed. When staff are knowledgeable about picking strategies and motivated by incentives, they’re more likely to minimise errors and work efficiently.
- Leverage Real-Time Data and Tracking: Using software like Lofko’s integrated tracking systems allows you to monitor every stage of the pick and pack process. With real-time updates on inventory levels, picking accuracy, and shipping statuses, you can quickly identify and resolve bottlenecks, ensuring a smooth fulfilment process.
By anticipating these challenges and implementing effective solutions, your business can transform potential obstacles into opportunities for improvement. This not only boosts efficiency and reduces costs but also ensures that you consistently meet customer expectations, building loyalty and trust in your brand.
Conclusion
Optimising the pick and pack process is essential for any ecommerce business aiming to grow, reduce costs, and exceed customer expectations. By implementing efficient strategies, leveraging technology like Lofko’s WMS, and following best practices, you can transform your fulfilment operations into a well-oiled machine that drives success.
Remember, the pick and pack process isn’t just about getting orders out the door quickly; it’s about ensuring accuracy, maintaining customer satisfaction, and ultimately enhancing your brand’s reputation. From optimising warehouse layouts and training your team to adopting automation and monitoring real-time performance, each step you take brings you closer to building a seamless and scalable fulfilment system.
By investing in the right tools and continuously refining your approach, your business can stay competitive in a fast-paced ecommerce market and deliver the kind of service that keeps customers coming back.
FAQs
- What is pick and pack?
- Pick and pack is a key part of the order fulfilment process in which products are picked from warehouse shelves and then packed for shipping. It involves collecting items from inventory based on customer orders and packaging them securely before dispatch.
- Why is the pick and pack process important for ecommerce businesses?
- The pick and pack process is crucial because it directly impacts delivery speed and order accuracy. An efficient process ensures customers receive their orders promptly and correctly, enhancing customer satisfaction and building brand loyalty.
- What are common picking strategies used in warehouses?
- Common picking strategies include piece picking (picking one order at a time), batch picking (picking multiple orders simultaneously), zone picking (picking products from specific zones), and wave picking (picking products from multiple zones at the same time). Each strategy is designed to optimise efficiency based on warehouse size and order volume.
- How can technology improve the pick and pack process?
- Technology like Warehouse Management Systems (WMS), such as Lofko, can automate inventory tracking, generate optimised picking routes, and provide real-time updates. This reduces errors, speeds up the picking and packing process, and ensures orders are shipped accurately and efficiently.
- What are the benefits of using the right-sized packaging in the pick and pack process?
- Using appropriately sized packaging minimises shipping costs by reducing cubic weight charges. It also helps protect products during transit, enhances the unboxing experience for customers, and reduces the environmental impact by using fewer materials.