The Complete Guide to Fulfil Orders: Strategies and Best Practices
02 Dec 2024
|by diadmin
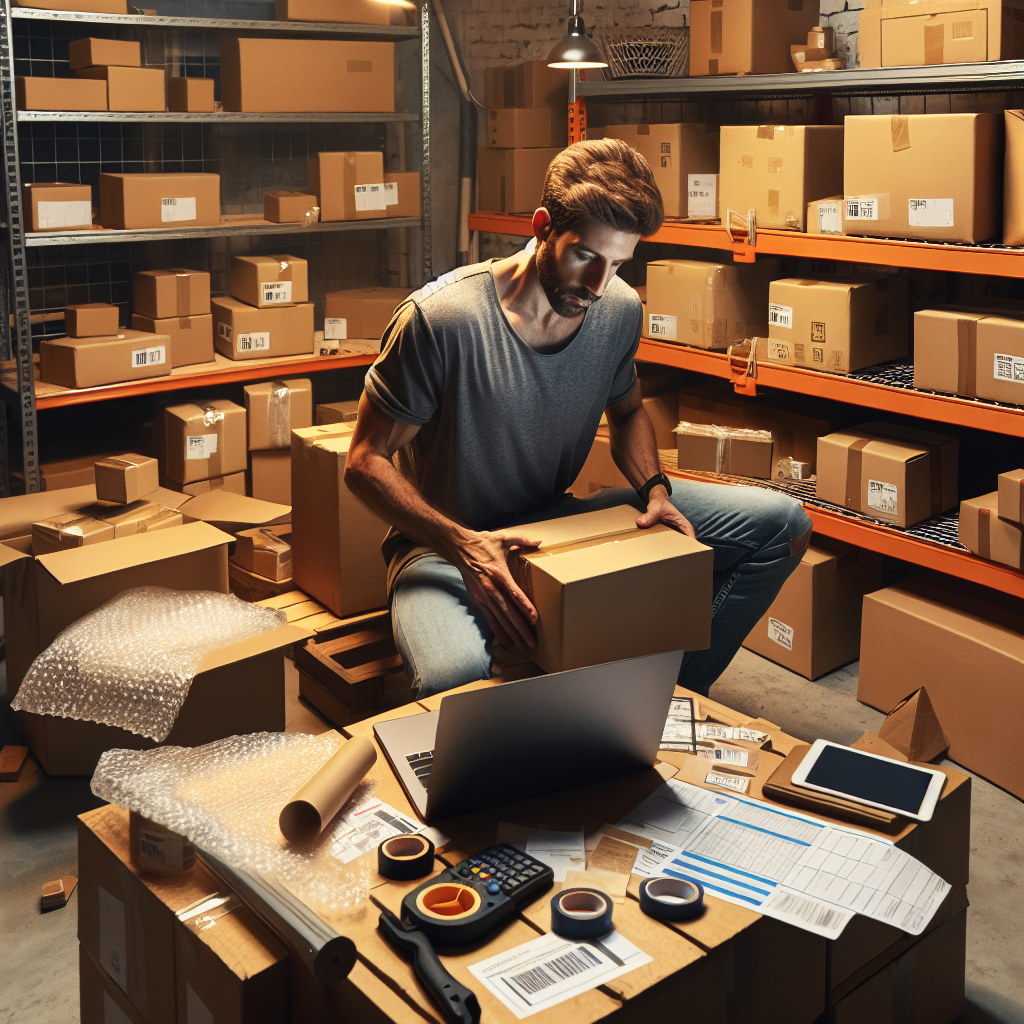
Mastering how to fulfil orders is vital for eCommerce success. Efficient order fulfilment means getting products to customers accurately and swiftly. This article offers actionable tips to help you optimize the process, improve customer satisfaction, and cut costs.
Key Takeaways
- Understanding the order fulfilment process is essential for optimizing efficiency, cutting costs, and enhancing customer satisfaction.
- Implementing automation and effective inventory management can significantly improve order processing and reduce fulfilment costs.
- Choosing the right fulfilment partner and leveraging advanced software are crucial steps in streamlining operations and ensuring timely deliveries.
Understanding the Order Fulfilment Process
Order fulfilment is pivotal to the triumph of eCommerce businesses, encompassing a sequence of actions that guarantee orders from customers are accurately and swiftly received, handled, and dispatched. This series comprises taking delivery of inventory, storing said inventory, processing customer orders as well as picking out items for those orders before packing them up for shipping and ultimately delivering them.
These stages are integral parts of managing the supply chain effectively by connecting customer needs with product dispatches. By refining these processes to fulfil orders, you can reduce costs related to fulfilment while simultaneously improving overall customer satisfaction and smoothing out business operations.
Receiving Inventory
The commencement of the order fulfilment journey is signalled by the receipt of inventory. Upon delivery to a fulfilment center, each item undergoes a thorough count and quality inspection. To ensure efficient organization and expedite order processing, it’s crucial that all items are meticulously documented with information like SKUs or barcodes.
Inventory may come from various sources including third-party suppliers, different departments within the company, or even from one’s own warehouses. It is imperative for receiving processes to be precise so as to accurately reflect inventory levels in records and position goods optimally for seamless access at the time of order picking.
Inventory Storage
Efficient supply chain management hinges on proper inventory storage, ensuring that the amount, placement, and condition of stock are meticulously monitored. This is vital for achieving optimal storage conditions. By allocating goods across several distribution centers, one can decrease shipping lengths and decrease expenses.
Utilizing methodologies such as the FIFO (first-in-first-out) approach and employing analytical tools in warehouses greatly enhances visibility into how frequently inventory cycles through a system while improving pick efficiency and the preciseness of fulfilled orders. Such strategies guarantee that products within an inventory are managed orderly and safely secured.
Order Processing
The phase of order processing plays a crucial role as it involves the reception, confirmation, execution, and assignment of orders to inventory stock. By consolidating all orders within one unified system, both productivity is boosted and a uniform workflow is maintained.
Employing no-code automation for directing orders can notably expedite the order management process by minimizing mistakes and holdups. An efficient order management system facilitates automatic distribution according to the availability of inventory and expense considerations, guaranteeing prompt dispatches to patrons.
Picking and Packing Orders
Retrieving particular items from stock and getting them ready for dispatch is the essence of picking and packing. Employing prevalent techniques such as discrete, zone, and batch order picking can amplify productivity.
To fulfil orders the process of packing requires securing goods with protective packaging to safeguard against harm while in transit, along with affixing labels that provide shipping details and tracking identifiers. Engaging third-party logistics (3PL) partners to handle the packing tasks can diminish manual workloads and heighten efficiency. Conversely, companies opting to pack their products internally benefit from being able to tailor their packaging according to their brand’s unique requirements.
Fulfil Orders Implementing Shipping and Delivery
The concluding phase of the order fulfilment process encompasses shipping and delivery, which involves tasks such as producing shipping labels, opting for suitable carriers, and giving customers access to track their shipments. Ensuring timely deliveries at reduced shipping costs hinges on selecting the correct shipping method and effectively organizing logistics.
Collaborating with a range of carriers including United States Postal Service (USPS), UPS, FedEx, and DHL enables an assortment of convenient solutions along with extensive service outreach. Promptness in delivering orders without errors plays a vital role in upholding elevated levels of customer satisfaction and fostering enduring loyalty.
The Importance of Efficient Order Fulfilment
Optimising efficiencies to fulfil orders is not only about prompt deliveries. It also improves customer experience and the efficiency of operations. In a fierce eCommerce environment, refined fulfilment processes are critical for increasing customer retention and encouraging repeat purchases.
Evaluating performance indicators and selecting an appropriate fulfilment centre ally can revolutionize operations within fulfilment centres, diminish expenses, and enhance precision. As online shopping numbers swell in Australia, companies must focus on operational efficiency to satisfy the rising expectations of customers.
Impact on Customer Experience
Rapid and precise processing of orders is pivotal to ensuring customer satisfaction. Discrepancies in inventory management and protracted durations for handling returns can culminate in dissatisfied customers and forfeited opportunities for sales. Implementing robust quality control measures along with straightforward return policies can significantly improve the overall experience for customers.
In the context of Australian online shoppers, offering complimentary shipping services stands out as a key incentive influencing their purchasing decisions. By guaranteeing swift and reliable delivery, businesses can secure a competitive edge within the marketplace.
Cost Implications
Efficiently organized fulfilment practices greatly enhance profit margins through the reduction of fulfilment expenses. The automation of order processing not only slashes labour costs but also augments safety within the work environment. Optimal logistics management, which encompasses selecting an appropriate shipping method and carrier, achieves a balance between delivery speed and expense, guaranteeing prompt deliveries without incurring high costs.
Prioritizing cost savings empowers companies to redirect funds into various segments of their business, fostering expansion and establishing a competitive edge in their industry.
Common Challenges in Order Fulfillment
Due to the high volume of orders and intricate logistics, ecommerce businesses encounter distinct difficulties in executing effective ecommerce order fulfilment. The fulfilment process can become complex when dealing with numerous shipping providers and diverse delivery schedules. Frequent complications arise from shortages in supply, challenges related to inventory management, and missteps in logistical coordination.
When scaling their operations, these issues may pose substantial obstacles for ecommerce companies striving to sustain proficient and precise order fulfillment.
Managing Inventory Levels
Ensuring that inventory levels are maintained at the perfect equilibrium is a fine art. Depletion of inventory can result in unhappy customers and damage to the reputation of a brand, while excessive stock leads to increased storage costs and other related expenses.
Implementing robust systems for precise monitoring and forecasting demand helps avoid both excesses and shortages of stock. Conducting consistent physical checks along with employing digital solutions guarantees reliable data on inventory quantities, aiding companies in proficiently managing their inventories.
Handling Returns
Maintaining operational efficiency and ensuring customer satisfaction are both crucial, which can be achieved through proficient management of the return handling process. This encompasses reverse logistics, where returned products make their way back to retailers or manufacturers. Offering multiple return methods such as mail-in or in-store options increases convenience for customers.
Utilizing cutting-edge returns management software helps organize RMA transactions and coordinate returns effectively, minimizing mistakes and refining the overall procedure of returning items. The implementation of uniform procedures for processing exchanges and returns aids in simplifying operations while enhancing efficiency.
Different Order Fulfillment Models
Different business requirements and scales require various order fulfilment strategies, such as in-house processing, third-party logistics (3PL), or utilising drop shipping. Each of these models has its benefits and potential obstacles tailored to the specific needs of a company.
By understanding the distinctions among these fulfilment options, companies can select the most appropriate method for enhancing their order processing operations.
In-House Fulfillment
Managing fulfilment internally, known as in-house fulfilment, involves handling the entire process without external support. This approach enables companies to maintain tighter control over their procedures and expenses, and it can be more economical for those dealing with a small volume of orders.
Yet when order volumes grow, the difficulties associated with overseeing in-house fulfilment may escalate markedly. This could require a business to either scale up its operations or engage the services of a third-party logistics provider to manage these increased demands.
Third-Party Logistics (3PL)
Outsourcing logistics and fulfilment responsibilities to an outside service provider is third-party logistics (3PL). Companies entrust 3PL providers with critical tasks like storage, inventory management, and transportation. This delegation allows companies to focus on their primary competencies while enhancing operational efficiency and elevating the quality of fulfilment.
Choosing a 3PL partner requires a clear understanding of cost structures and services provided. Transparency in these areas is essential for making an informed decision.
Dropshipping
In the dropshipping fulfilment model, companies do not keep products in stock. Instead, when an order is made, it’s forwarded to a third-party supplier who then sends the item directly to the customer. This method is particularly advantageous and cost-efficient for small businesses since it eliminates the need to invest in inventory.
Because merchants rely on external suppliers for order fulfilment, they exercise less control over this process. This lack of oversight can affect how satisfied customers are with their shopping experience.
Strategies to Improve Order Fulfillment
To enhance operational efficiency and streamline processes, particularly in order fulfilment, businesses need to persistently observe their practices and adopt innovative approaches. Utilizing data analytics, implementing automation, and encouraging employee participation are vital actions for improvement. Acknowledging incremental progress with rewards, engaging staff at the outset of adopting new systems, and investing in modern technology are crucial steps towards achieving this goal.
Optimize Inventory Management
Preventing stockouts and excess inventory is essential for efficient inventory management. Utilizing data analytics can improve the forecasting of customer demand, leading to the optimization of inventory levels. Systems that manage inventories in real-time offer immediate visibility into current stock amounts, facilitating precise monitoring and effective storage of inventory.
By adopting this method, problems such as backorders can be avoided, which in turn boosts operational efficiency within the management systems dealing with inventories.
Automate Order Processing
Incorporating automation into the fulfilment process can substantially decrease labour expenses and enhance work conditions. These systems are adept at managing customer order tracking, executing the processing of orders, and generating shipping labels automatically, thereby maintaining seamless operations throughout high-demand periods.
The adoption of automated solutions in businesses allows for a reduction in human errors while boosting the efficiency with which orders are fulfilled.
Enhance Picking and Packing Efficiency
Improving efficiency in the picking and packing stages requires implementing organized strategies and formal techniques. Utilizing clear and legible labels helps in precise sorting, as well as ensuring correct delivery, which notably minimizes mistakes within this workflow.
The integration of methodical picking practices alongside efficient labelling optimizes the fulfilment process as a whole, leading to enhancements in both pace and precision.
Leveraging Order Fulfillment Software
Software for order fulfilment streamlines operations by automating various tasks, increasing efficiency and minimizing human mistakes. This technology delivers instantaneous insights into inventory quantities and simplifies the workflow associated with processing orders to maintain precision while allowing for growth.
By forming connections with shipping carriers, this software grants enhanced oversight over the entire network of fulfilment. Such optimization leads to better-managed procedures, which ultimately elevate customer satisfaction levels.
Key Features to Look For
When selecting software for order fulfilment, ensure it includes capabilities such as live inventory tracking, the automation of order processing tasks, and integration across multiple sales channels. The ideal software should provide functions tailored to each platform it serves while maintaining uninterrupted operational coherence.
The inventory management system should be adaptable and customizable, enabling businesses to scale their operations up or down according to their expanding requirements without complications.
Integration with Sales Channels
By connecting fulfilment software with various sales channels, the process of order management is unified across different platforms, eliminating manual data entry. Direct integration with prominent platforms such as Shopify and Amazon, along with key marketplaces, guarantees accurate information in real-time and boosts operational efficiency.
This technology enhances support for fulfil orders through online sales avenues by optimizing the entire order fulfilment sequence. This guarantees that customers receive their purchases swiftly and reliably.
Choosing the Right Fulfillment Partner
Choosing an appropriate fulfilment partner is essential for being in sync with your business objectives and expansion strategies. It’s important to carry out comprehensive market research to pinpoint potential suppliers who meet your specific requirements and provide competitive rates.
Entrusting a dedicated provider can elevate operational efficacy. It’s imperative that this provider be trustworthy, have proficiency in inventory management, and prioritize the customer experience.
Monitoring and Improving Performance
Regular examination and enhancement of the fulfilment process are crucial for attaining targeted performance metrics. Consistently observing critical performance indicators (KPIs) enables companies to pinpoint which aspects require refinement, allowing them to modify their approach effectively.
Attending to issues that arise after implementation is vital for businesses to sustain seamless operations and increase total efficiency.
Quality Control Checks
To ensure high service standards and promote customer satisfaction, quality control measures are implemented throughout the fulfilment process to minimize mistakes and increase the accuracy of orders. By having different individuals responsible for picking and packing, the efficiency of these checks can be improved.
Using Data Analytics
By leveraging data analytics, companies can detect and rectify inefficiencies within the order fulfilment process, facilitating focused enhancements. Continuous monitoring of key performance indicators (KPIs) for order fulfillment is instrumental in recognizing operational constraints and refining procedures.
Utilizing analytical instruments offered by platforms such as Fulfil can elevate the efficacy of order processing and assess the effectiveness of various channels, thereby streamlining operations.
Case Study: Successful Order Fulfillment Transformation
The eCommerce company grappled with ensuring prompt deliveries and precise handling of orders. Regular instances of delayed shipments along with elevated return frequencies stemming from inaccuracies in the order processing, posed significant problems for the business. Through the integration of a sophisticated order management system paired with effective inventory tracking techniques, the organization revolutionized its fulfilment process.
Integrating automation within their picking and packing procedures diminished errors caused by manual intervention, while comprehensive training for staff facilitated a seamless transition to these advanced systems. These improvements culminated in substantial growth in punctual delivery rates, slashing returns by 25% and significantly enhancing ratings pertaining to customer satisfaction.
Future Trends in Order Fulfillment
The landscape of order fulfilment is undergoing significant changes due to new trends and technological advancements. Customized elements such as tailored packaging options and personalized recommendations are elevating the customer experience during the fulfilment process. In warehouse operations, voice-activated technology for order picking is becoming more prevalent, enabling workers to operate without using their hands by receiving auditory instructions they can confirm verbally.
These developments play a pivotal role in enhancing operational efficiency, while also catering to the dynamic expectations of customers.
Fulfil Orders Summary
Improving the order fulfilment process is crucial for boosting customer satisfaction and increasing operational efficiency. Businesses can streamline their operations and cut expenses by comprehensively grasping the intricacies of order fulfilment, tackling prevalent difficulties, and employing tactics that heighten efficiency. Essential elements to attain triumph include utilizing advanced order fulfilment software, selecting an appropriate partner for fulfilment tasks, and perpetually tracking performance metrics. By putting these methods into practice, companies will be equipped to satisfy escalating consumer expectations and maintain a competitive edge within the dynamic world of eCommerce.
Frequently Asked Questions
What are the main steps in the order fulfilment process?
The main steps in the order fulfilment process are receiving inventory, storing it, processing orders, picking and packing, followed by shipping and delivery.
Each step is crucial for ensuring an efficient and accurate fulfilment experience.
How does efficient order fulfilment impact customer satisfaction?
Efficient order fulfilment significantly boosts customer satisfaction by ensuring quick, accurate processing and timely deliveries. This leads to a smoother shopping experience and fosters customer loyalty.
What are the benefits of using a third-party logistics provider (3PL)?
Utilizing a third-party logistics provider enhances operational efficiency by handling warehousing, inventory management, and shipping, enabling businesses to concentrate on their core activities.
This leads to improved resource allocation and cost savings.
How can data analytics improve the Fulfil Orders process?
By leveraging data analytics, businesses can substantially improve the order fulfilment process through the identification and rectification of inefficiencies, as well as optimizing inventory levels. This leads to more streamlined operations and better performance metrics.
Utilizing these analytical insights leads to a fulfilment system that is both more efficient and effective in its operations.
What are some future trends in order fulfilment?
Personalisation in order fulfilment, along with advancements in voice-activated technology for order picking, are key trends shaping the future.
These innovations will enhance efficiency and better meet customer expectations. Talk to us and ask how we may be able to help.