The Ultimate Guide to Stock Take: Best Practices and Procedures
23 Dec 2024
|by diadmin
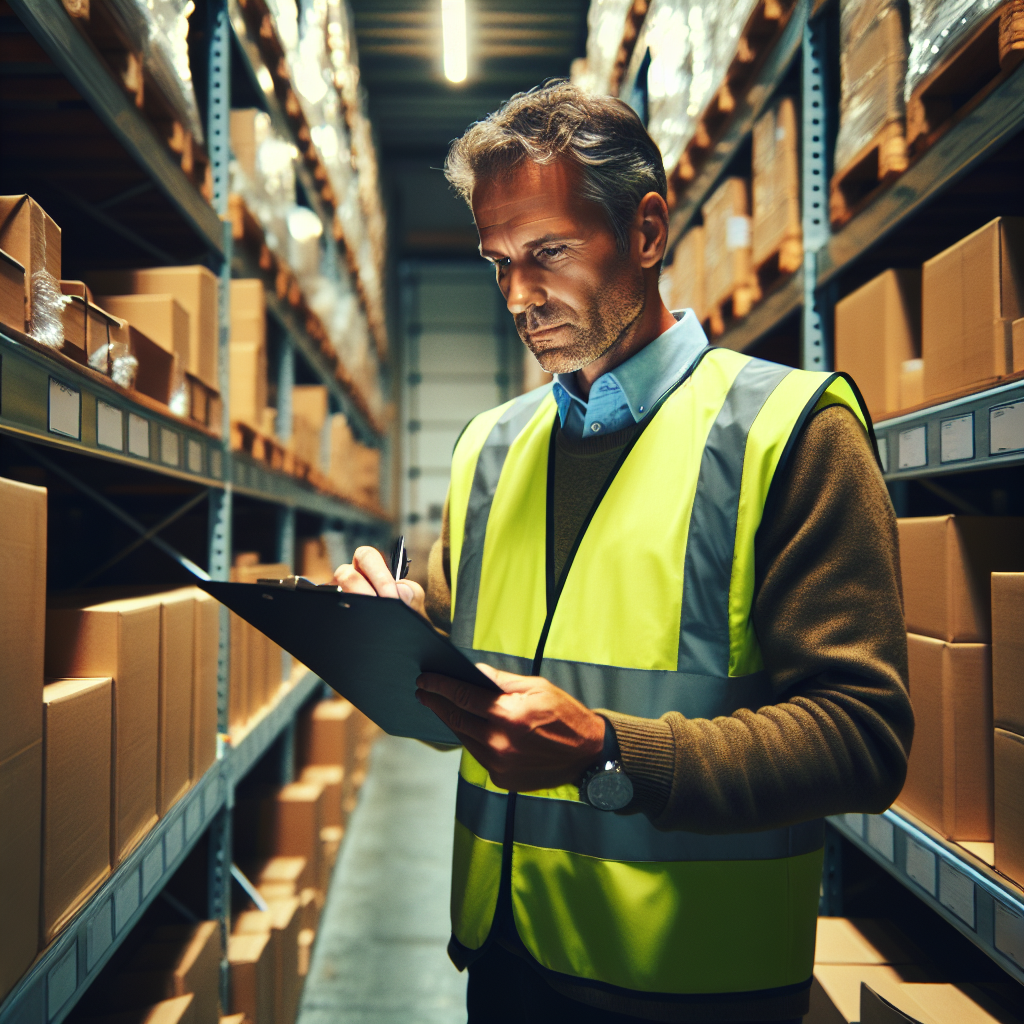
Running a business without a firm grip on your inventory is like navigating in the dark. Without an accurate stock take, you risk stockouts, over-ordering, or theft, leading to lost sales, extra costs, and unhappy customers. Inconsistent or outdated records can disrupt efficiency, hurt profits, and prevent timely order fulfillment.
Analyzing inventory data allows businesses to identify fast-moving and slow-moving products, thereby optimizing purchasing decisions and reducing unnecessary storage costs.
Imagine missing a big sale because you thought you had enough stock, only to find your records were wrong. Discovering major discrepancies too late can lead to bigger issues, affecting cash flow, damaging reputation, and hindering growth.
Proper stocktaking provides a clear view of your inventory, aiding smart decisions on buying, production, and sales. This guide covers everything you need, from the basics and benefits of stocktaking to best practices for an efficient stocktake. Using these strategies, you’ll gain control over your stock, streamline operations, cut losses, and set your business up for success.
What is a Stock Take?
A Stock Take, also called inventory checking or stock counting, is the process of physically verifying the quantity and condition of inventory items in a business. It’s a key aspect of inventory management, ensuring that inventory records match actual stock levels. By regularly conducting a stock take, businesses can identify stock discrepancies, such as missing items or damaged goods, and take steps to maintain optimal inventory levels. This practice helps avoid issues like overordering or stockouts, which can affect cash flow and customer satisfaction.
Though stocktaking can be time-consuming, especially for larger operations, it’s essential for maintaining inventory accuracy and making informed decisions. Whether it’s an annual stocktake, cycle count, or spot check, stocktaking provides a reliable snapshot of physical inventory. This accuracy enables businesses to optimise inventory management, reduce waste, and maximise sales opportunities while ensuring their inventory system remains efficient and up-to-date.
Why Is Stock Taking Important?
Stocktaking is vital for maintaining accurate inventory records and ensuring that the physical stock levels match what’s recorded in your inventory management system. By regularly conducting stocktakes, businesses can identify discrepancies, such as missing items, damaged stock, or theft, and address these issues promptly. This not only helps maintain optimal inventory levels but also prevents costly mistakes like overordering or stockouts, which can disrupt operations and affect customer satisfaction.
Beyond accuracy, stocktaking supports informed decision-making. With a clear picture of existing stock, businesses can better plan for purchasing, production, and sales, ensuring that resources are allocated efficiently. It also helps businesses comply with auditing and regulatory requirements, making stocktaking an essential practice for improving overall inventory control, optimising inventory management, and maximising profitability.
The 6 Key Benefits of Stock Takes For Your Business
Regular stock takes provide businesses with a reliable way to manage inventory by offering an accurate, real-time view of their stock levels. Here are six key advantages of stock taking:
Accurate Inventory Records
Stock takes ensure that physical stock levels match your inventory records, reducing discrepancies such as missing, damaged, or obsolete items. This helps maintain inventory accuracy and reliability.
Informed Decision-Making
With accurate stock data, businesses can make better decisions about purchasing, production, and sales, ensuring they have the right amount of stock on hand without overstocking or understocking.
Prevention of Losses
Stock takes help identify issues like theft, stock shrinkage, and damages early on, allowing for immediate corrective action and minimising financial losses.
Optimisation of Inventory Levels
Regular stock takes enable businesses to maintain optimal inventory levels, which reduces the risk of stockouts, prevents overordering, and frees up cash flow.
Improved Supply Chain Efficiency
By knowing exactly how much stock is available, businesses can streamline their supply chain processes, reduce waste, and ensure that stock items move efficiently through the system.
Enhanced Customer Satisfaction
Accurate inventory management means products are available when customers need them, leading to better order fulfilment, reduced delivery delays, and an overall improved customer experience.
Stock takes are essential for businesses looking to optimise inventory management processes, reduce waste, and maximise sales opportunities, making them a critical part of any inventory management strategy.
Preparing for a Stock Take
Proper preparation is the foundation of a successful stocktake. By ensuring that your location, inventory, and team are ready, you can minimise disruptions, avoid errors, and ensure accurate results. Here’s how to get your business prepared for the stocktake:
Organise Your Inventory
Before the stocktake, it’s essential to organise your stockroom or warehouse. Ensure that all stock items are properly labeled and categorised, with similar items grouped together. This makes it easier to physically count your inventory and reduces the chances of confusion or miscounts. Don’t forget to locate any misplaced items, so your actual stock levels match your inventory records.
Ensure Stock Records Are Up to Date
Double-check that your inventory records are current before the stocktake begins. You’ll want to include any recent deliveries, sales, or returns that may not yet be reflected in the system. This step is key to avoiding stock discrepancies and ensuring an accurate count.
Gather Necessary Tools and Materials
Make sure you have all the equipment needed for the stocktake, such as barcode scanners, calculators, stock sheets, and mobile devices. If you’re using cloud-based software, ensure it’s set up to streamline the process, reduce human error, and save time when counting physical stock.
Assign Roles and Responsibilities
Organise your team by clearly defining who will count which section or type of inventory. Assign specific areas or tasks to each team member to ensure accountability and prevent overlap. Consider their familiarity with the stock area and inventory system for a more efficient count.
Plan for Business Disruptions
A stocktake can be time-consuming and potentially disruptive to normal operations. Plan to conduct the stocktake at a time that minimizes disruption, such as after hours or during a slower business period. If you anticipate needing extra hours, ensure that your staff is available and prepared.
By thoroughly preparing for the stocktake, you can streamline the process, reduce the chances of error, and ensure accurate results. Proper organisation and preparation will allow your business to optimise inventory management and make more informed decisions moving forward.
Understanding the Stock Take Process
The stocktaking process is essential for ensuring that your inventory records accurately reflect your physical stock levels. By following a structured approach, businesses can minimise discrepancies, optimise stock control, and make informed decisions based on real data. Here’s a step-by-step breakdown of the stocktaking process:
- Planning How You’ll Perform the Stocktake:
Plan ahead to choose the most suitable time for the stocktake, ideally during off-peak hours to avoid disrupting regular operations. Determine the type of stocktake (e.g., annual stocktake, cycle count) and communicate the schedule to all relevant team members.
- Preparing Your Location and Organising Inventory:
Organise the stockroom, store, or warehouse by ensuring all inventory items are clearly labelled and arranged systematically. This preparation reduces the risk of human error and makes it easier for staff to count stock accurately.
- Gathering Necessary Materials and Assigning Responsibilities:
Collect the necessary tools, such as barcode scanners, stock sheets, calculators, and any cloud-based software used for inventory tracking. Assign roles to staff, designating specific areas or inventory categories for each team member to cover, ensuring accountability and consistency during the stocktake.
- Conducting a Pre-Count:
Perform a pre-count to identify any obvious discrepancies or errors in your existing inventory records before the full stocktake. This step allows you to correct inaccuracies in advance and reduces confusion during the main count.
- Performing the Initial Stocktake:
Physically count the entire inventory systematically, either manually or using barcode scanners for greater accuracy. Follow a consistent counting method (e.g., left to right or top to bottom) to ensure all items are checked. Record each item accurately on the stock sheets or within your inventory management system.
- Recounting Discrepancies That Do Not Match Your Stock Records:
If there are discrepancies between the physical count and inventory records, conduct a recount of those specific items. This step helps to confirm whether the discrepancy is due to human error or an actual stock issue, like shrinkage or misplaced items.
- Updating Inventory Records:
Once the stocktake is complete, update your inventory records to reflect the actual stock levels found during the count. This ensures your inventory system is accurate, providing a reliable basis for making decisions about purchasing, production, and sales.
By following these structured steps, businesses can maintain accurate stock levels, reduce errors, and improve their overall inventory management processes, leading to better efficiency and customer satisfaction.
Stock Taking Methods
When it comes to conducting a stocktake, businesses can choose from several methods depending on their specific needs and the size of their inventory. Each method has its pros and cons, and selecting the right one can make a significant difference in terms of accuracy and efficiency. Here are the three most common stock taking methods:
Wall-to-Wall Stocktaking
This method involves counting the entire inventory at once, often done annually or semi-annually. Every item in the warehouse, stockroom, or store is physically counted, recorded, and compared to existing inventory records. While this method provides a complete view of stock levels, it can be time-consuming and often requires shutting down operations temporarily. It’s commonly used by businesses that prefer a periodic and comprehensive inventory check.
Cycle Counting
Instead of counting all stock at once, cycle counting involves counting a subset of your inventory at regular intervals. For example, a small business might count different categories of inventory each month. This method is less disruptive to daily operations and helps maintain accurate stock levels throughout the year. It’s an excellent choice for businesses looking to keep their inventory management system consistently up-to-date without the need for a full stocktake.
Spot Checking
Spot checking is a more random approach where specific stock items or areas are checked on an ad-hoc basis. Businesses may perform spot checks if they suspect stock discrepancies in certain inventory items or categories. This method can be helpful to identify and address stock discrepancies quickly without conducting a full stocktake, but it may not provide a complete picture of your inventory levels.
Each method has its own merits, so choosing the right one depends on your business type, the complexity of your inventory, and how frequently you want to ensure inventory accuracy. Whether you opt for an annual stocktake, regular cycle counting, or random spot checks, adopting a consistent stocktaking method is essential for maintaining optimal inventory levels and avoiding issues like missing orders, overstocking, or stockouts.
6 Best Practices To Improve Your Stock Take
There’s no one-size-fits-all approach to stocktaking, but there are plenty of ways to refine the process and improve how you record stock. Here are six practical tips to get you started.
Use Barcode Scanners to Minimize Errors
Manually counting stock increases the risk of human error, especially as your business expands. Incorporating barcode scanning technology simplifies the process, allowing you to quickly capture and log stock levels. With a light source and sensor, barcode scanners let you record large amounts of data swiftly and accurately, streamlining your inventory management.
Take Regular Breaks to Maintain Focus
Stocktaking can be mentally and physically exhausting. To avoid mistakes and keep your team sharp, plan regular breaks throughout the process. This will help maintain attention to detail and ensure the count is as accurate as possible.
Eliminate Distractions
Distractions like phones or background noise can lead to overlooked details or miscounts. Create an environment where your team can focus, reducing the likelihood of errors. A distraction-free setting helps you complete the stocktake faster and with fewer mistakes.
Keep Your Warehouse Organised
A cluttered stockroom is a recipe for confusion and delays during stocktaking. Keeping your warehouse neat and organized, with clear labeling and designated areas for different items, ensures that the stocktake proceeds smoothly. A well-managed stockroom also makes it easier to identify discrepancies or missing items.
Involve Your Team for a Smoother Process
Engage your team throughout the stocktaking process, especially those who handle inventory daily. Their input is invaluable in making sure everything runs smoothly. After the stocktake, ask for their feedback to improve the process for next time. A collaborative approach will ensure a more accurate and efficient count.
Adopt Cloud-Based Inventory Management Software
Switching to cloud-based inventory software like Lofko can revolutionize your stocktaking process. Real-time inventory tracking reduces your dependency on manual stocktakes, ensuring accurate stock levels are automatically maintained. Pairing this with barcode scanners allows you to automate many tasks, saving time and reducing human error. Lofko’s cloud-based platform also offers features such as inventory optimization, purchase order management, and multichannel sales integration, giving you a comprehensive solution to inventory control.
Ready to take your stocktaking to the next level? Lofko provides everything you need to streamline the process, enhance inventory accuracy, and save valuable time.
Stocktaking Frequency and Inventory Management
Determining Optimal Frequency
Determining the optimal frequency for stocktaking is crucial for effective inventory management. The frequency of stocktaking depends on various factors, including the type of business, inventory turnover, and storage space. For instance, businesses dealing with high-value or low-turnover items may require more frequent stocktakes to ensure accuracy and prevent losses. Conversely, those with fast-moving items might find less frequent stocktakes sufficient. A general rule of thumb is to perform stocktakes at least once a year, but this can vary depending on the specific needs of the business.
Regular stocktakes help businesses stay on top of their inventory, ensuring that stock levels are accurate and up-to-date. By tailoring the frequency of stocktakes to the unique demands of your business, you can maintain better control over your inventory and avoid common pitfalls like overstocking or stockouts.
Impact on Inventory Management
Regular stocktaking has a profound impact on inventory management. It helps businesses to:
- Maintain Accurate Inventory Records: Regular stocktakes ensure that your inventory records reflect the actual stock levels, reducing discrepancies and errors.
- Identify Discrepancies and Errors: By comparing physical stock with inventory records, businesses can quickly spot and address discrepancies, such as missing items or data entry errors.
- Optimize Inventory Levels: Regular stocktakes help maintain optimal stock levels, reducing the risk of stockouts and overstocking, and freeing up cash flow.
- Improve Inventory Turnover: Accurate stock records enable better forecasting and purchasing decisions, leading to improved inventory turnover and reduced deadstock.
- Enhance Supply Chain Efficiency: Knowing your exact stock levels allows for more efficient supply chain management, reducing waste and ensuring timely order fulfillment.
By performing regular stocktakes, businesses can ensure that their inventory management system is accurate and up-to-date. This accuracy is essential for making informed decisions, optimizing inventory levels, and driving business growth.
Outsourcing Stocktaking
Benefits of Outsourcing
Outsourcing stocktaking can be a cost-effective and efficient way to manage inventory. Here are some key benefits of outsourcing stocktaking:
- Reduced Labor Costs and Increased Productivity: Outsourcing stocktaking can reduce the need for in-house staff to perform time-consuming inventory counts, allowing them to focus on core business activities.
- Improved Accuracy and Reduced Errors: Professional stocktaking services use advanced technology and experienced personnel to ensure accurate counts, minimizing the risk of human error.
- Enhanced Inventory Management and Control: Outsourcing provides access to specialized expertise and technology, leading to better inventory control and management.
- Increased Flexibility and Scalability: Outsourcing allows businesses to scale their stocktaking efforts up or down based on their needs, providing greater flexibility.
- Access to Specialized Expertise and Technology: Professional stocktaking firms have the tools and knowledge to conduct efficient and accurate stocktakes, leveraging the latest technology and best practices.
By outsourcing stocktaking, businesses can free up resources and focus on core activities, while ensuring that their inventory management system is accurate and up-to-date. However, it’s essential to choose a reputable and experienced outsourcing partner to ensure that the stocktaking process is carried out efficiently and effectively.
Outsourcing stocktaking can be a strategic move for businesses looking to optimize their inventory management processes. By leveraging the expertise and technology of professional stocktaking services, businesses can achieve greater accuracy, efficiency, and control over their inventory, ultimately leading to improved profitability and growth.
Common Challenges and Risks in Stock Taking
While stock taking is essential for effective inventory management, it’s not without its challenges. Here are some common issues businesses face during the process and ways to mitigate them.
- Disruption to Daily Operations
Conducting a stocktake can cause interruptions in normal business activities, especially if done during working hours. This is particularly challenging for smaller businesses that can’t afford downtime. The best way to manage this is by planning stocktakes during off-peak hours or slow periods, ensuring minimal disruption. - Inaccurate Stock Counts
Human error is a major risk during stocktaking, whether due to manual counting mistakes or miscommunication among team members. These inaccuracies can lead to incorrect stock records, impacting future purchasing decisions and stock control. Implementing barcode scanners or counting software can reduce human error and improve accuracy. - Customer Impact
If stocktakes are not well-coordinated, they can lead to delayed shipments or inaccurate order fulfillment, affecting customer satisfaction. Planning your stocktake around order fulfillment schedules can help prevent delays, and outsourcing or automating stock management tasks can also minimize this risk. - Stock Discrepancies
Discrepancies between physical stock and inventory records are a common issue and can occur due to theft, misplacement, or data entry errors. Regular stocktakes, along with implementing inventory management systems like Lofko, can help identify these discrepancies sooner and ensure accurate stock levels are maintained. - Decreased Staff Engagement
Stocktaking can be a repetitive and time-consuming task, which may lead to disengagement among staff, resulting in further inaccuracies. To combat this, ensure your team understands the importance of accurate counts, offer incentives, and rotate tasks to maintain focus and morale.
By addressing these challenges head-on and adopting tools like Lofko’s cloud-based inventory system, businesses can reduce disruptions, improve accuracy, and maintain optimal inventory levels with ease.
Ready to take control of your business’s stock take? Sign up for a 30 day free trial with Lofko here
Conclusion
Stock taking is a vital part of effective inventory management, helping businesses maintain accurate inventory records and make informed decisions about purchasing, sales, and production. By following best practices, choosing the right methods, and leveraging technology like Lofko, businesses can streamline their stocktaking process, minimize errors, and optimize stock levels. Regular stocktakes, combined with proper planning and efficient inventory systems, reduce the risk of discrepancies, improve customer satisfaction, and ensure business operations run smoothly. Ultimately, a well-executed stocktake supports better inventory control, saving time, resources, and maximizing overall profitability.
Frequently Asked Questions
1. How often should I conduct a stocktake?
It depends on the size and nature of your business. For most companies, an annual or biannual stocktake is standard. However, businesses with high inventory turnover may benefit from more frequent stocktakes, such as quarterly or monthly. Implementing cycle counting can also help maintain continuous inventory accuracy without needing to count the entire stock all at once.
2. What’s the best way to reduce errors during stock takes?
Utilizing technology such as barcode scanners and inventory management systems like Lofko can drastically reduce human error. Ensuring your staff is well-trained, taking regular breaks during stocktakes, and keeping your stockroom organized are also important for accuracy.
3. Can I conduct a stocktake without disrupting daily business?
Yes, planning ahead is key. Conduct your stocktakes during off-peak hours or slower periods. If that’s not possible, consider splitting the task into smaller, manageable sections or using a cycle counting method to avoid large-scale disruptions.
4. What should I do if there are stock discrepancies?
When discrepancies arise, recount the items to ensure accuracy. Investigate possible causes such as theft, misplacement, or data entry errors. Updating your records promptly and using an inventory management system like Lofko will help prevent future discrepancies and maintain more accurate stock levels.
5. How can I improve my stocktaking process?
Improvement starts with planning and organization. Involving your team, reducing distractions, and using the right tools like barcode scanners and cloud-based inventory systems can enhance efficiency. Periodically reviewing and refining your procedures based on feedback and results will also keep the process streamlined.